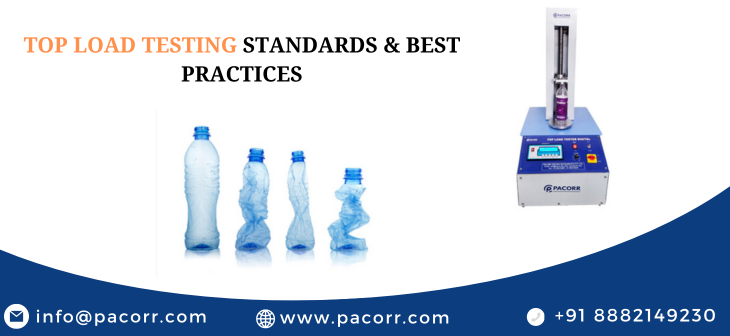
Top load testing, crucial in assessing the structural integrity of packaging containers, involves applying a downward force to a product to determine its resistance to deformation or failure. This test is vital for manufacturers who need to ensure their packaging can withstand stacking during shipping and storage. Commonly tested items include plastic bottles, cardboard boxes, and metal cans, where the strength and flexibility of the packaging are paramount.
Key Standards in Top Load Testing
ASTM D4169-16
ASTM D4169-16, a standard practice for performance testing of shipping containers and systems, outlines the procedures for simulating real-world forces, conditions, and impacts that are likely to occur during shipping and handling. This standard is integral for manufacturers looking to comply with international shipping regulations and to ensure product safety and integrity.
ISO 12048
ISO 12048, also known as the "Packaging — Complete, filled transport packages — Compression and stacking tests using a compression tester," provides guidelines on how to perform compression tests on packaging. It helps manufacturers determine the compressive strength, stackability, and the load a package can bear before experiencing a structural failure.
ISTA 3A
ISTA 3A standard is designed for single parcel shipment testing. It focuses on packages that weigh 150 lbs or less, which are prepared for delivery to end-users from parcel delivery services. The tests include a series of drop tests, compression tests, and vibration tests to ensure the package can handle the rigors of courier handling and transit environments.
TAPPI T804
TAPPI T804 covers the compression testing of fiberboard shipping containers. It assesses the container's ability to resist external compressive loads during transit and storage. This standard is crucial for ensuring that fiberboard boxes, which are commonly used in bulk shipments, maintain their integrity and protect the contents throughout the supply chain.
Best Practices for Effective Top Load Testing
1. Understand Product Vulnerabilities:
Start by analyzing where your product may be most vulnerable during transit. Understanding these points helps in setting realistic test parameters that mimic actual stress conditions the product will face.
2. Use the Right Equipment:
It's essential to use the correct testing equipment to obtain accurate results. Pacorr’s Top Load Tester is an exemplary piece of equipment designed for this purpose. It offers precise measurements and can simulate various environmental conditions that a package might face during transit.
3. Consistent Test Environment:
Maintain a consistent testing environment to ensure that the test results are reliable and replicable. Variations in temperature or humidity can affect the outcome and lead to inaccurate data.
4. Compliance with Standards:
Adhering to relevant standards such as ASTM D4169-16, ISO 12048, ISTA 3A, and TAPPI T804 ensures that the testing process meets international guidelines and that the results are recognized globally.
5. Regular Reviews and Updates:
Regularly review and update testing procedures to incorporate new packaging materials, designs, and technology advancements. This proactive approach ensures ongoing compliance and relevance in rapidly changing market conditions.
Top Load Testing for Bottles
Top load testing is an essential quality control measure for bottle manufacturers to ensure their products can withstand the compressive forces they will encounter during filling, capping, handling, stacking, and transportation. The process assesses the bottle's ability to resist deformation or failure under load, which is vital to avoid product loss, safety hazards, and brand reputation damage.
Key Considerations in Bottle Top Load Testing
1. Material and Design Influence:
The material (plastic, glass, metal) and design of the bottle significantly influence its strength and the type of testing required. Plastic bottles, for example, are often tested for both axial load and radial compression to simulate the forces experienced during capping and stacking.
2. Testing Parameters:
Parameters such as the speed of compression, the height from which the bottle is compressed, and the duration of applied load are critical. These parameters need to be adjusted based on the bottle's material, shape, and intended use to simulate real-world conditions accurately.
3. Standard Compliance:
Adhering to relevant standards ensures that the bottle will perform as expected in its lifecycle. For bottles, standards such as ASTM D4169-16 for distribution simulation and ISO 12048 for stacking strength are particularly relevant.
Pacorr’s Top Load Tester – A Closer Look
Pacorr offers a sophisticated Top Load Tester that is ideal for conducting top load testing on bottles. Here’s how it benefits bottle testing:
- Precision and Accuracy: The tester is designed to deliver highly accurate and repeatable results, which is essential for ensuring consistent bottle quality.
- Digital Display and Control: It features a digital display that provides precise control over the test parameters and clear visibility of the test results, facilitating ease of use and data collection.
- Adjustability: The equipment can accommodate different sizes and shapes of bottles, making it versatile for various products.
- Compliance with Standards: Pacorr’s tester meets global standards, helping manufacturers ensure compliance and acceptance in international markets.
Best Practices for Bottle Top Load Testing
- Pre-Testing Analysis: Conduct a thorough analysis of the bottle design and the conditions it will face during its lifecycle. This step helps in setting up the test parameters more accurately.
- Environment Simulation: Where possible, simulate the environmental conditions (like temperature and humidity) that the bottles will face during storage and transportation to understand how these factors might affect the integrity of the bottles.
- Regular Calibration and Maintenance: Ensure that the testing equipment is regularly calibrated and maintained to prevent any discrepancies in test results caused by faulty equipment.
By focusing on thorough testing and using advanced equipment like Pacorr's offerings, manufacturers can assure customers and regulators of their commitment to quality and safety. This attention to detail not only protects the product but also supports the brand's reputation for reliability and consumer safety.
Tailored Top Load Testing for Different Bottle Types
1. Plastic Bottles
Plastic bottles, commonly made from materials like PET (polyethylene terephthalate), HDPE (high-density polyethylene), or PVC (polyvinyl chloride), require specific considerations:
- Test Environment: The flexibility of plastic means that temperature can significantly affect its strength. Tests should simulate a range of environmental conditions to ensure bottles maintain integrity across varied climates.
- Loading Technique: The distribution of force is crucial, especially for softer plastics. A uniform force application ensures that the bottle's response to compression is accurately measured, mimicking how bottles are stacked during shipping.
2. Glass Bottles
Glass bottles are highly rigid but also more brittle than plastic, necessitating a different testing approach:
- Impact of Shape: The shape of a glass bottle can greatly influence its load-bearing capacity. Rounded shapes may handle compressive forces better than angular designs with stress points.
- Speed of Compression: The rate at which compression is applied during testing should simulate real-world scenarios. Sudden loads can reveal vulnerabilities in glass bottles that gradual loads might not.
3. Metal Cans
Although not typically referred to as "bottles," metal cans are an essential part of the packaging spectrum that might also require top load testing, especially for beverages:
- Material Thickness: The thickness of the metal can affect its ability to withstand top loads. Thinner cans may be easier to stack but are more susceptible to deformation.
- End Seals: The integrity of the seals at both ends of metal cans is crucial. Testing should include end-load bearing to ensure the seals do not fail under compression.
Advanced Features of Pacorr’s Top Load Tester
Pacorr’s Top Load Tester is equipped with advanced features that make it exceptionally suitable for handling the diverse needs of different bottle types:
- Versatility: The device can adjust to fit various bottle sizes and shapes, allowing for comprehensive testing across product lines.
- Precision Force Application: It offers precise control over how force is applied, crucial for testing delicate containers like glass bottles where uneven force application can cause breakage.
- Digital Monitoring: Real-time data capture and digital monitoring allow for immediate adjustments and detailed analysis, ensuring that every test is both accurate and reproducible.
Best Practices Revisited for Specific Bottles
- Continuous Testing: Regular testing throughout the product development and production phases ensures consistent bottle quality from batch to batch.
- Prototype Testing: Before full-scale production, conduct top load testing on prototypes to refine the design based on test outcomes.
- Competitor Benchmarking: Analyze how competitor bottles perform under similar tests to identify strengths and areas for improvement in your own products.
Conclusion
Top load testing is a nuanced process that varies significantly with the type of bottle being tested. By understanding the specific needs of different materials and shapes, manufacturers can better prepare their products to withstand the rigors of storage and transport. Pacorr’s Top Load Tester provides a comprehensive solution that meets these varied needs with precision and adaptability, ensuring that all types of bottles maintain their integrity under pressure.
Thanks to Pacorr Testing instruments, we have all the required quality testing instruments that have helped us to ensure the best quality delivered to our clients.
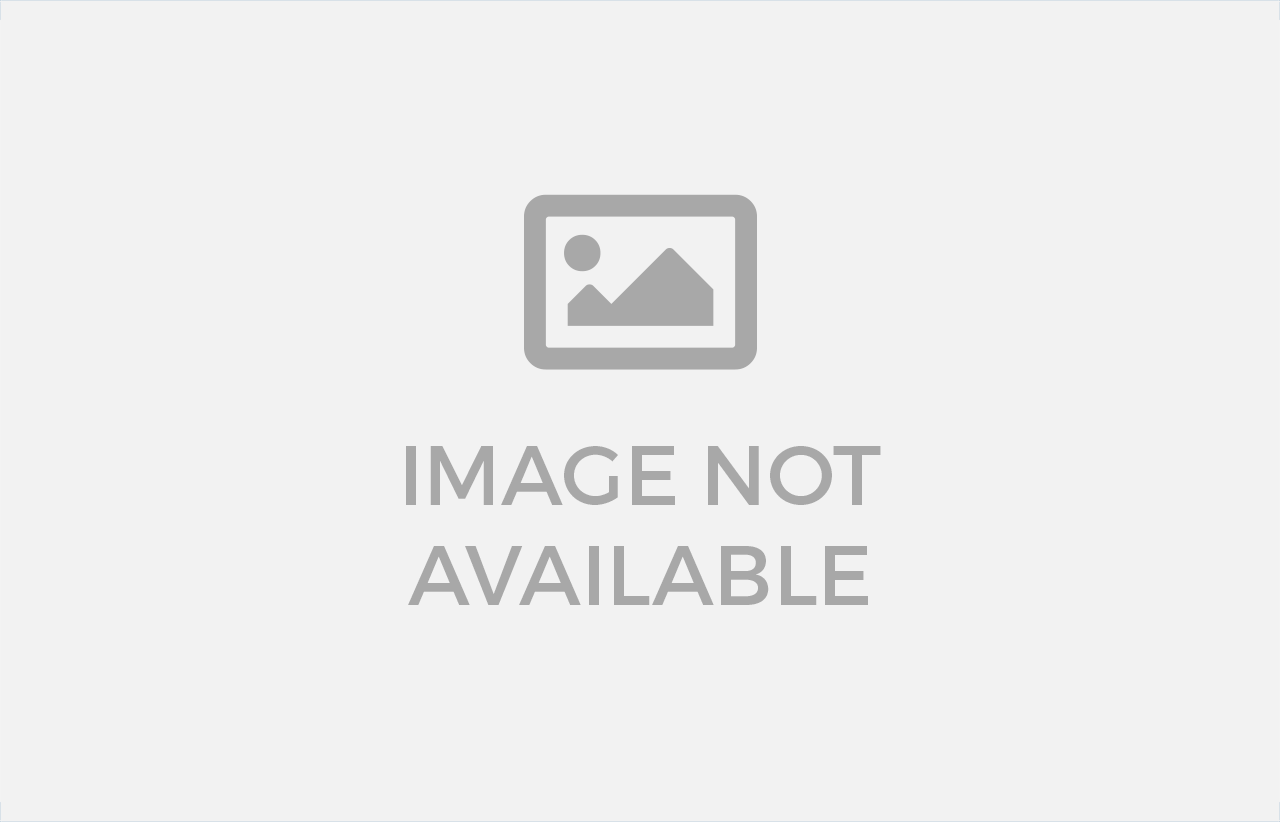
Danish
Fair Exports Pvt. Ltd.