.png)
Salt spray testing is a crucial process in various industries to assess the corrosion resistance of a material and coating. This comprehensive guide covers the ins and outs of salt spray testing, its benefits, applications, and more. Let’s dive into the details!
How Does a Salt Spray Test Work?
Salt spray testing involves placing a test specimen in a chamber where it is exposed to a saline mist at a controlled temperature. This environment simulates the corrosive conditions materials might face in real-world settings. The test aims to accelerate the corrosion process, providing quick and reliable data on the material’s durability.
Key Components:
- Salt Solution: Typically, a 5% sodium chloride solution.
- Chamber: A sealed cabinet where the salt spray is generated.
- Nozzle: To disperse the salt solution as a fine mist.
- Heating System: Maintains the chamber temperature, usually around 35°C (95°F).
Benefits of Salt Spray Testing
Salt spray testing offers numerous benefits, making it a go-to method for corrosion testing.
- Quick Results: Accelerates corrosion, providing data faster than natural exposure.
- Standardized Testing: Follows international standards like ASTM B117, ensuring consistency.
- Cost-Effective: Relatively low-cost compared to long-term environmental exposure tests.
- Versatility: Suitable for various materials, including metals, coatings, and plastics.
- Predictive Analysis: Helps predict long-term corrosion behavior and product lifespan.
Applications of Salt Spray Chambers
A salt spray chamber finds applications across diverse industries due to its effectiveness in simulating corrosive environments.
- Automotive Industry: Evaluating the corrosion resistance of car parts and coatings.
- Aerospace: Testing aircraft components to ensure they withstand harsh atmospheric conditions.
- Marine Industry: Assessing materials and coatings used in ships and offshore structures.
- Electronics: Ensuring the durability of electronic components exposed to corrosive environments.
- Construction: Testing building materials and protective coatings for durability.
Salt Spray Chamber Maintenance Tips
Regular maintenance of a salt spray chamber is crucial to ensure accurate and reliable test results.
- Regular Cleaning: Clean the chamber interior and nozzle to prevent salt buildup.
- Check Solution Levels: Ensure the salt solution is at the correct concentration and volume.
- Inspect Components: Regularly inspect the nozzle, heating system, and other parts for wear and tear.
- Calibration: Regularly calibrate the chamber to maintain accuracy.
- Environmental Controls: Monitor and control the humidity and temperature inside the chamber.
How to Interpret Salt Spray Test Results
Interpreting salt spray test results requires understanding the correlation between test conditions and real-world scenarios.
- Visual Inspection: Look for signs of corrosion like rust, pitting, or blistering.
- Weight Loss Measurement: Measure the weight loss of the specimen to quantify corrosion.
- Microscopic Analysis: Examine the microstructure for any degradation or damage.
- Compare with Standards: Align results with industry standards to determine pass/fail status.
- Time to Failure: Assess the time it takes for corrosion to appear, indicating material performance.
Salt Spray Chamber Calibration Procedures
Calibration is essential to maintain the accuracy and reliability of a salt spray chamber.
- Temperature Calibration: Use a calibrated thermometer to ensure the chamber maintains the correct temperature.
- Solution Concentration: Regularly test the concentration of the salt solution.
- Spray Rate: Calibrate the nozzle to ensure the spray rate is consistent with standards.
- Pressure Check: Ensure the air pressure in the chamber is within the specified range.
- Documentation: Keep detailed records of calibration procedures and results.
Common Issues with Salt Spray Tests
Despite their utility, salt spray tests can encounter several issues that may affect results.
- Nozzle Blockage: Salt buildup can clog the nozzle, affecting spray distribution.
- Inconsistent Temperature: Fluctuations in chamber temperature can lead to inaccurate results.
- Solution Contamination: Impurities in the salt solution can alter test conditions.
- Corrosion of Chamber Parts: Chamber components themselves can corrode, impacting the environment.
- Incorrect Calibration: Improper calibration can lead to unreliable results.
Salt Spray Test Standards and Regulations
Salt spray testing adheres to various standards to ensure uniformity and reliability.
- ASTM B117: The most widely used standard for salt spray testing.
- ISO 9227: An international standard for salt spray tests.
- DIN 50021: A German standard outlining specific test procedures.
- JIS Z 2371: A Japanese standard for corrosion tests.
- BS EN 60068-2-11: A British standard for environmental testing.
Environmental Impacts of Salt Spray Testing
While beneficial, salt spray testing has environmental considerations.
- Waste Management: Proper disposal of used salt solutions to prevent environmental contamination.
- Energy Consumption: High energy use for maintaining chamber conditions.
- Chemical Use: Handling and disposal of chemicals need careful management to avoid pollution.
- Equipment Lifespan: Regular maintenance to extend equipment lifespan and reduce waste.
Salt Spray Chamber vs. Humidity Chamber
Both salt spray and humidity chambers are used for environmental testing, but they serve different purposes.
- Salt Spray Chamber: Focuses on corrosion resistance using saline mist.
- Humidity Chamber: Tests material performance under various humidity levels without saline exposure.
- Applications: Salt spray for corrosion, humidity chambers for material behavior under moisture.
- Test Conditions: Salt spray involves a corrosive environment, humidity chambers simulate humid conditions.
- Result Interpretation: Salt spray results focus on corrosion, humidity chamber results on material stability.
Summary
Salt spray testing is a critical method for assessing the corrosion resistance of a material across various industries. Understanding how these tests work, their benefits, and their applications can help ensure the longevity and durability of products. Regular maintenance and calibration of a salt spray chamber are essential to obtain accurate and reliable results. By adhering to established standards and regulations, industries can make informed decisions about material performance and environmental impact.
For more in-depth insights and professional guidance on salt spray testing, visit Pacorr's website and explore our comprehensive range of testing solutions.
Thanks to Pacorr Testing instruments, we have all the required quality testing instruments that have helped us to ensure the best quality delivered to our clients.
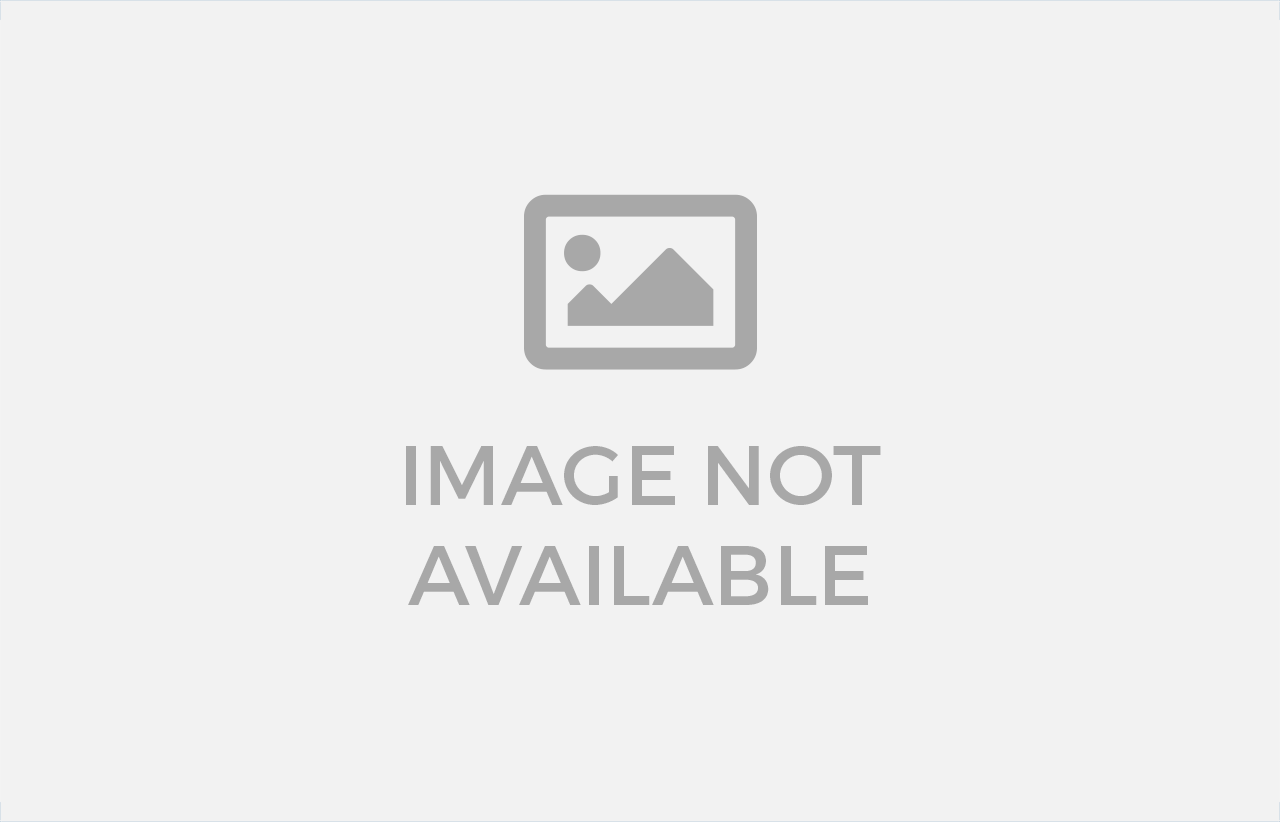
Danish
Fair Exports Pvt. Ltd.