
That's where the Pacorr Drop Test comes into play a pivotal assessment for evaluating the impact resistance of packages during handling and shipping. To help you navigate this essential testing procedure, we've compiled an insightful guide incorporating standards like IS:7028 Pt IV, TAPPI T802, and ASTM D 5276, which define the methodology for conducting reliable drop tests.
5 Essential Factors to Consider Before Performing a Pacorr Drop Test
Before you begin drop testing, it's critical to understand these five factors to ensure accurate and useful results:
- Test Environment: Control and monitor the environment, such as temperature and humidity, as specified by IS:7028 Pt IV to mimic real-world conditions.
- Sample Preparation: Prepare your samples consistently to avoid variability in results.
- Drop Height Selection: Depending on your product type, select an appropriate drop height as guided by TAPPI T802.
- Impact Surfaces: Use a flat and rigid surface that meets ASTM D 5276 standards to ensure the impact is realistic.
- Data Recording: Equip yourself with the right tools to accurately measure and record the outcomes of the test.
Top 5 Industries That Need the Pacorr Drop Test
The Pacorr Drop Test is indispensable across various sectors, notably:
- Electronics Manufacturing: Emphasize the importance of drop testing for consumer electronics like smartphones, laptops, and tablets, which are frequently at risk of being dropped by users.
- Packaging Industry: Highlight how drop testing ensures that various types of packaging can withstand the rigors of shipping and handling, which is crucial for maintaining the integrity of the product inside.
- Toy Manufacturing: Discuss the role of drop testing in ensuring the durability of toys, particularly those intended for younger children, to ensure they can withstand rough play without breaking.
- Furniture Manufacturing: Explain how drop testing is used to assess the durability and structural integrity of furniture items, ensuring they can handle the weight and usage over time without failure.
- Automotive Parts Manufacturing: Detail how critical components, especially those made of glass or brittle materials, are tested for their ability to survive impacts, contributing to overall vehicle safety.
7 Common Mistakes to Avoid in Pacorr Drop Testing
Avoid these pitfalls to enhance the reliability of your drop tests:
- Inconsistent sample handling.
- Ignoring manufacturer’s guidelines.
- Overlooking the importance of repeat tests.
- Failing to document the test setups and results.
- Not using calibrated equipment.
- Disregarding the influence of external environmental factors.
- Skipping post-test inspections.
4 Key Benefits of Using Pacorr Drop Tests for Product Safety
Implementing Pacorr Drop Tests can bring forth several advantages:
- Improved Product Design: Insights from tests can lead to sturdier packaging.
- Customer Satisfaction: Ensuring product integrity reduces complaints and returns.
- Compliance with Standards: Adhering to international standards enhances market credibility.
- Cost Efficiency: Reducing product damage cuts significant potential losses.
6 Steps to Conduct a Successful Pacorr Drop Test
Follow these steps to execute an effective drop test:
- Define the objective based on your industry requirements.
- Select appropriate test samples as per IS:7028 Pt IV standards.
- Setup the drop test apparatus according to ASTM D 5276 guidelines.
- Perform the test, maintaining strict adherence to the protocol.
- Analyze the data with an eye towards continuous improvement.
- Document every step and result for future reference and compliance.
Stories of Success and Innovation
My First Experience with the Pacorr Drop Test: A Case Study
When first implementing the Pacorr Drop Test, the insights gained significantly altered our approach to packaging, turning initial skepticism into trust in the process's value.
How Pacorr Drop Testing Saved Our Product Line
After several product failures in transit, integrating Pacorr Drop Tests helped us redesign our packaging, drastically reducing damage rates and saving our reputation.
The Day We Improved Our Packaging Standards with Pacorr Drop Tests
Transitioning to standards-guided testing transformed our QA processes, leading to superior product quality and customer trust.
Overcoming Shipping Damages: A Success Story with Pacorr Drop Tests
Adopting rigorous drop testing protocols helped us overcome a major challenge of shipping damages, leading to improved logistics and customer satisfaction.
Innovating Durability: How We Integrated Pacorr Drop Tests into Our QA Process
Embedding drop tests into routine quality checks fostered a culture of innovation and durability that set new industry benchmarks.
Opinions on Pacorr Drop Testing
Why Pacorr Drop Tests Are Essential for Ensuring Product Durability
These tests are not just procedures but are crucial for verifying that products can endure the physical stresses of the shipping process.
Is the Pacorr Drop Test the Most Effective Way to Test Impact Resistance?
While highly effective, it's one part of a comprehensive testing strategy that includes other methods to ensure complete product evaluation.
The Pros and Cons of Pacorr Drop Testing in Manufacturing
While invaluable for improving packaging, the time and resources involved can be considerable.
Can Pacorr Drop Tests Replace Traditional Durability Checks?
While not a replacement, they are a significant enhancement, providing specific insights that other tests may not offer.
How Pacorr Drop Tests Are Shaping the Future of Product Safety
As industries evolve, these tests are becoming a cornerstone of product development, ensuring safety and durability from the design phase through to customer delivery.
A Framework for Future Testing
Planning Your Product Testing: Incorporating Pacorr Drop Tests
Incorporating drop tests into your testing protocols ensures a robust product testing strategy that can significantly reduce the risk of product failures in the market.
Understanding and implementing Pacorr Drop Tests according to the guidelines provided by standards such as IS:7028 Pt IV, TAPPI T802, and ASTM D 5276 not only enhances product safety but also bolsters consumer confidence in your products. By integrating these tests into your quality assurance processes, you pave the way for higher standards of durability and reliability in your products, leading to greater market success and consumer trust.
What People Say
Thanks to Pacorr Testing instruments, we have all the required quality testing instruments that have helped us to ensure the best quality delivered to our clients.
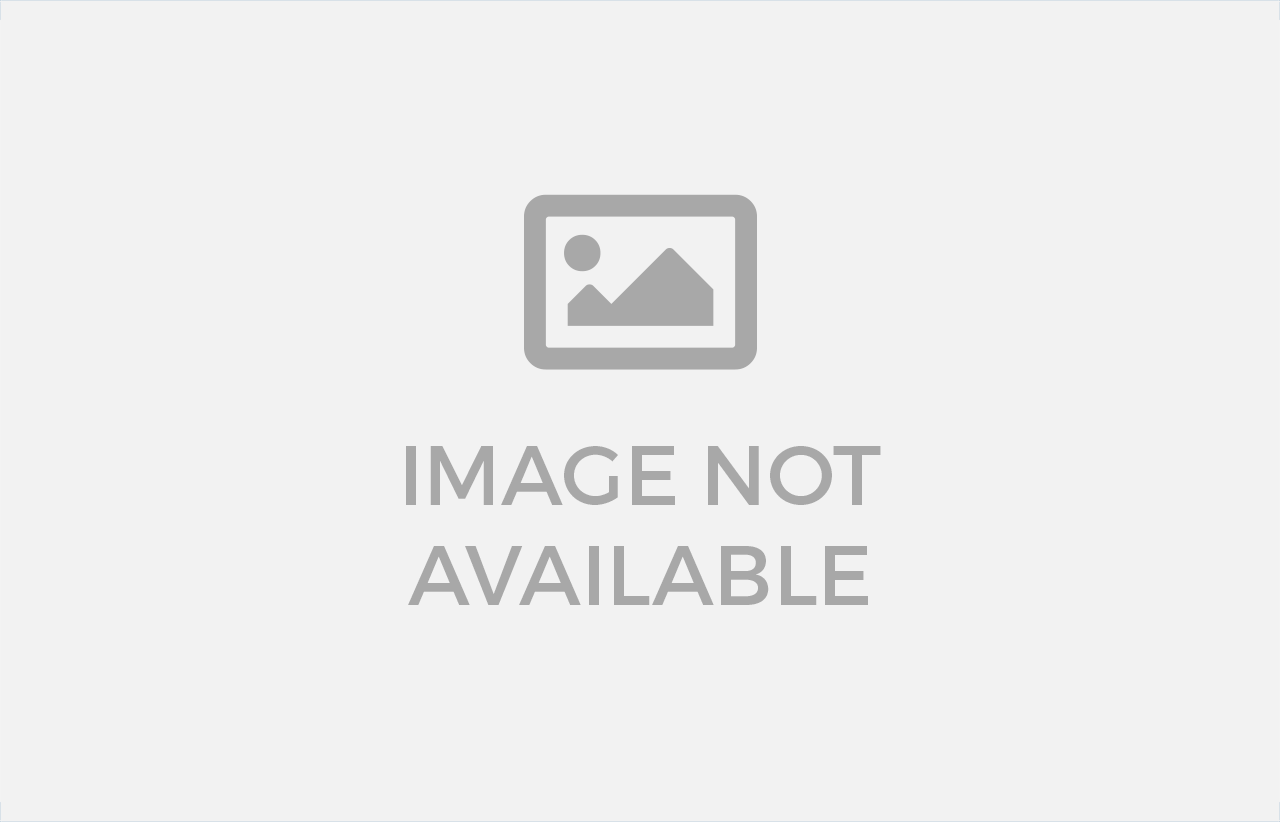
Danish
Fair Exports Pvt. Ltd.