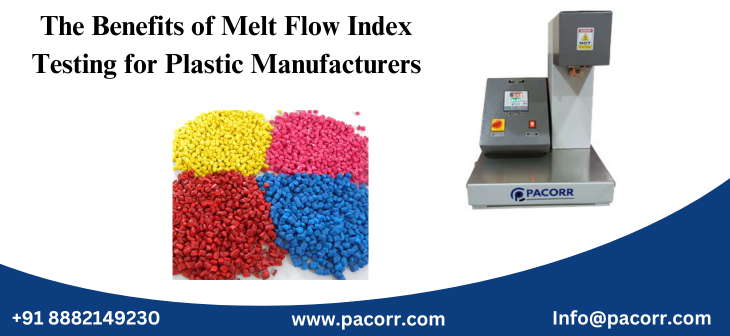
A melt flow index (MFI) tester is an essential device in the polymer industry, specifically designed to measure the melt flow rate (MFR) of thermoplastic polymers. This device plays a critical role in determining the flow properties of plastic materials when they are in a molten state. The melt flow rate is an indicator of how easily a polymer can flow when subjected to heat and pressure, which is vital information for quality control, material selection, and processing operations in the plastic manufacturing industry.
The MFI tester operates by heating a polymer sample to a specified temperature within a barrel. Once the polymer reaches this temperature and becomes molten, a defined weight is applied, forcing the polymer through a standardized die. The rate at which the polymer extrudes through the die is then measured and recorded as the melt flow rate, typically expressed in grams per 10 minutes. This measurement provides valuable insight into the polymer's viscosity and molecular structure, helping manufacturers understand and predict the material's behavior during processing.
Offered by Pacorr, MFI testers are renowned for their precision and reliability. These devices are equipped with advanced features that ensure accurate measurements, such as precise temperature control, automated weight application, and user-friendly interfaces. Pacorr’s MFI testers are designed to meet industry standards, ensuring that the measurements are consistent and comparable across different testing scenarios.
The significance of using a melt flow index tester cannot be overstated. It helps manufacturers maintain consistent quality in their products by providing a reliable method for assessing the flow properties of thermoplastics. This is crucial for applications where precise material properties are required, such as in automotive, aerospace, packaging, and consumer goods industries. By using an MFI tester, manufacturers can optimize their processes, reduce material waste, and ensure that their products meet stringent quality standards.
How to Use a Melt Flow Index Tester
Using a melt flow index tester involves a systematic process that ensures accurate and repeatable measurements of the polymer’s melt flow rate. The first step in using an MFI tester is to prepare the polymer sample. This typically involves cutting the sample into small pieces to fit into the tester’s barrel. Ensuring the sample is clean and free from contaminants is crucial, as impurities can affect the accuracy of the test results.
Once the sample is prepared, it is loaded into the barrel of the MFI tester. The barrel is then heated to a predetermined temperature specific to the polymer being tested. This temperature must be controlled precisely, as even small deviations can lead to significant errors in the melt flow rate measurement. Pacorr’s MFI testers are equipped with advanced temperature control systems that ensure the barrel maintains the correct temperature throughout the testing process.
After the sample has reached the desired temperature and is fully molten, a specified weight is applied to the material. This weight forces the molten polymer through a die with a standardized opening. The weight applied and the dimensions of the die are standardized according to industry specifications, such as ASTM D1238 or ISO 1133, to ensure consistent and comparable results. The extruded polymer is collected and its mass is measured over a specified time period, usually ten minutes.
The melt flow rate is calculated by dividing the mass of the extruded polymer by the time period, resulting in a measurement expressed in grams per 10 minutes. This value provides critical information about the polymer’s flow characteristics. Pacorr’s MFI testers simplify this process with automated features that handle the timing and measurement, reducing the potential for human error and increasing the repeatability of the tests.
It is important for users to follow the operating instructions provided with their MFI tester to ensure accurate results. Regular maintenance and calibration of the equipment are also essential to maintain its accuracy and reliability over time. Pacorr provides comprehensive support and training for users, ensuring that they can operate the MFI tester effectively and confidently.
Benefit of Using a Melt Flow Index Tester
The benefits of using a melt flow index tester in the plastic manufacturing industry are manifold. One of the primary advantages is the ability to assess the flow properties of thermoplastic polymers quickly and accurately. This assessment is crucial for quality control, material selection, and optimizing processing conditions. By measuring the melt flow rate, manufacturers can gain valuable insights into the viscosity and molecular structure of their materials, enabling them to produce high-quality products consistently.
A significant benefit of using an MFI tester is the improved quality control it offers. Consistency in the melt flow rate indicates that the polymer will behave predictably during processing, leading to uniformity in the final product. This is particularly important in industries where precise material properties are critical, such as automotive, aerospace, and medical devices. By using Pacorr’s MFI testers, manufacturers can ensure that their plastic materials meet industry standards and perform reliably in their intended applications.
Another advantage is the optimization of processing conditions. Understanding the melt flow rate of a polymer allows manufacturers to fine-tune their processing parameters, such as temperature, pressure, and cooling rates, to achieve optimal results. This can lead to increased efficiency, reduced material waste, and lower production costs. For instance, a polymer with a high melt flow rate may require lower processing temperatures, reducing energy consumption and improving cycle times.
Using an MFI tester also facilitates material selection. Different applications require materials with specific flow properties, and the melt flow rate is a key factor in determining the suitability of a polymer for a particular use. By measuring the MFR, manufacturers can select the right material for their needs, ensuring that the final product has the desired characteristics. Pacorr’s MFI testers provide precise and reliable measurements, helping manufacturers make informed decisions about material selection.
Furthermore, the use of an MFI tester can enhance compliance with industry standards. Many industries have stringent regulations regarding the properties of plastic materials, and compliance with these standards is essential for market acceptance. By using a reliable MFI tester, manufacturers can ensure that their materials meet the required specifications, facilitating regulatory compliance and market entry.
In summary, the benefits of using a melt flow index tester are numerous and significant. From improving quality control and optimizing processing conditions to facilitating material selection and ensuring regulatory compliance, an MFI tester is an invaluable tool in the plastic manufacturing industry. Pacorr’s MFI testers are designed to deliver accurate and reliable results, providing manufacturers with the insights they need to produce high-quality plastic products consistently.
Melt Flow Index Tester Calibration
Calibration of a melt flow index tester is a critical process that ensures the accuracy and reliability of the measurements obtained from the device. Regular calibration is necessary to maintain the precision of the tester and to ensure that the results are consistent and comparable over time. Calibration involves verifying and adjusting the key components of the MFI tester, such as the temperature control system, weight application mechanism, and measurement sensors.
The first step in calibrating a melt flow index tester is to check the temperature control system. The temperature of the barrel must be accurately controlled to match the specified test conditions. Even small deviations in temperature can lead to significant errors in the melt flow rate measurement. Calibration involves using a calibrated temperature probe to measure the actual temperature inside the barrel and compare it to the set temperature. Any discrepancies are adjusted to ensure that the temperature control system is accurate.
Next, the weight application mechanism is calibrated. The applied weight must be precise and consistent to ensure accurate measurement of the melt flow rate. Calibration involves using standard reference weights to verify that the applied weight matches the specified value. Any deviations are adjusted to ensure that the weight application mechanism is functioning correctly.
The measurement sensors and timing systems also require calibration. These components are responsible for measuring the mass of the extruded polymer and the time period over which the measurement is taken. Calibration involves using standard reference materials with known melt flow rates to verify the accuracy of the measurement sensors. The timing system is checked to ensure that it accurately measures the specified time period.
Pacorr provides comprehensive calibration services and guidelines to help users maintain the accuracy and reliability of their MFI testers. These services include detailed instructions for performing calibration, as well as access to calibrated reference materials and tools. Pacorr’s MFI testers are designed with features that facilitate easy calibration, such as accessible calibration ports and user-friendly interfaces.
Regular calibration is essential to ensure the long-term accuracy and reliability of a melt flow index tester. It helps to identify and correct any issues that may affect the performance of the device, ensuring that the measurements obtained are accurate and consistent. By maintaining a calibrated MFI tester, manufacturers can ensure that their quality control processes are reliable and that their products meet industry standards.
In conclusion, the calibration of a melt flow index tester is a vital process that ensures the accuracy and reliability of the device. Pacorr’s comprehensive calibration services and guidelines help users maintain their MFI testers in optimal condition, providing accurate and consistent measurements for quality control and material selection. Regular calibration is essential for maintaining the precision of the MFI tester and ensuring the quality and consistency of plastic products.
Understanding Melt Flow Index Results
Interpreting melt flow index results is crucial for understanding the flow properties of thermoplastic polymers and making informed decisions about material selection and processing conditions. The melt flow rate (MFR) provides valuable information about the polymer’s viscosity and molecular structure, which can influence its behavior during processing and in the final application.
A higher melt flow rate indicates that the polymer has a lower viscosity and higher flowability. This means that the material will flow more easily when subjected to heat and pressure. Polymers with high MFR are typically used in applications that require easy flow and molding, such as injection molding and extrusion processes. However, high MFR can also indicate a lower molecular weight, which may affect the mechanical properties of the final product.
Conversely, a lower melt flow rate indicates that the polymer has a higher viscosity and lower flowability. This means that the material will flow less easily when subjected to heat and pressure. Polymers with low MFR are typically used in applications that require higher mechanical strength and durability, such as automotive parts and structural components. Low MFR can also indicate a higher molecular weight, which can enhance the toughness and impact resistance of the material.
Understanding the relationship between MFR and polymer properties is essential for material selection. For instance, in applications where high flowability is required, such as thin-walled parts or complex molds, a polymer with a high MFR would be preferred. On the other hand, in applications where mechanical strength and durability are critical, such as load-bearing components, a polymer with a low MFR would be more suitable.
Pacorr’s melt flow index testers provide precise and reliable MFR measurements, enabling users to make informed decisions based on the material’s flow characteristics. These testers are designed to comply with industry standards, ensuring that the results are consistent and comparable across different testing scenarios.
Interpreting MFR results also involves considering the specific requirements of the application and the processing conditions. For example, a high MFR polymer may require lower processing temperatures and pressures, which can reduce energy consumption and improve cycle times. However, it may also require careful control of the molding process to avoid defects such as flashing or sink marks. Similarly, a low MFR polymer may require higher processing temperatures and pressures, which can increase energy consumption and cycle times, but may also result in better mechanical properties and surface finish.
In conclusion, understanding melt flow index results is essential for making informed decisions about material selection and processing conditions. The MFR provides valuable insights into the polymer’s viscosity and molecular structure, which can influence its behavior during processing and in the final application. Pacorr’s MFI testers provide accurate and reliable MFR measurements, helping users to optimize their processes and ensure the quality and consistency of their products.
Melt Flow Index Testing Process
The melt flow index testing process is a standardized method used to determine the melt flow rate (MFR) of thermoplastic polymers. This process provides critical data on the material’s viscosity and flow properties, which are essential for quality control, material selection, and optimizing processing conditions. The melt flow index test is conducted according to specific standards, such as ASTM D1238 and ISO 1133, which ensure consistency and comparability of results.
The first step in the melt flow index testing process is to prepare the polymer sample. The sample is typically cut into small pieces to fit into the tester’s barrel. It is important to ensure that the sample is clean and free from contaminants, as impurities can affect the accuracy of the test results.
Once the sample is prepared, it is loaded into the barrel of the melt flow index tester. The barrel is then heated to a predetermined temperature specific to the polymer being tested. This temperature must be controlled precisely, as even small deviations can lead to significant errors in the melt flow rate measurement. Pacorr’s MFI testers are equipped with advanced temperature control systems that ensure the barrel maintains the correct temperature throughout the testing process.
After the sample has reached the desired temperature and is fully molten, a specified weight is applied to the material. This weight forces the molten polymer through a die with a standardized opening. The weight applied and the dimensions of the die are standardized according to industry specifications, such as ASTM D1238 or ISO 1133, to ensure consistent and comparable results. The extruded polymer is collected and its mass is measured over a specified time period, usually ten minutes.
The melt flow rate is calculated by dividing the mass of the extruded polymer by the time period, resulting in a measurement expressed in grams per 10 minutes. This value provides critical information about the polymer’s flow characteristics. Pacorr’s MFI testers simplify this process with automated features that handle the timing and measurement, reducing the potential for human error and increasing the repeatability of the tests.
It is important for users to follow the operating instructions provided with their MFI tester to ensure accurate results. Regular maintenance and calibration of the equipment are also essential to maintain its accuracy and reliability over time. Pacorr provides comprehensive support and training for users, ensuring that they can operate the MFI tester effectively and confidently.
In conclusion, the melt flow index testing process is a standardized method used to determine the melt flow rate of thermoplastic polymers. This process provides critical data on the material’s viscosity and flow properties, which are essential for quality control, material selection, and optimizing processing conditions. Pacorr’s MFI testers are designed to facilitate this process with features such as precise temperature control, easy sample loading, and automated measurement systems, ensuring reliable and accurate results.
Common Problems with a Melt Flow Index Tester
Common problems with a melt flow index tester can affect the accuracy and reliability of the measurements, leading to incorrect conclusions about the material’s properties. Understanding these potential issues and how to address them is essential for maintaining the performance of the tester and ensuring accurate results.
One of the most common problems with melt flow index testers is temperature inconsistencies. The temperature of the barrel must be precisely controlled to match the specified test conditions. Even small deviations in temperature can lead to significant errors in the melt flow rate measurement. Temperature inconsistencies can be caused by a malfunctioning temperature control system, incorrect calibration, or external factors such as ambient temperature fluctuations. Pacorr’s MFI testers are equipped with advanced temperature control systems that ensure the barrel maintains the correct temperature throughout the testing process. Regular calibration and maintenance of the temperature control system are essential to prevent temperature inconsistencies.
Another common problem is improper weight application. The weight applied to the molten polymer must be precise and consistent to ensure accurate measurement of the melt flow rate. Improper weight application can be caused by a malfunctioning weight application mechanism, incorrect calibration, or user error. It is important to regularly check and calibrate the weight application mechanism to ensure that it is functioning correctly. Pacorr provides comprehensive calibration services and guidelines to help users maintain the accuracy and reliability of their MFI testers.
Sample contamination is another common problem that can affect the accuracy of melt flow index measurements. Contaminants such as dust, dirt, or moisture can affect the flow properties of the polymer, leading to incorrect measurements. It is important to ensure that the sample is clean and free from contaminants before testing. Pacorr’s MFI testers are designed with easy-to-clean components that minimize the risk of sample contamination.
User error is another potential issue that can affect the accuracy of melt flow index measurements. This can include incorrect sample preparation, improper loading of the sample into the barrel, or incorrect operation of the tester. It is important for users to follow the operating instructions provided with their MFI tester to ensure accurate results. Pacorr provides comprehensive support and training for users, ensuring that they can operate the MFI tester effectively and confidently.
In conclusion, common problems with melt flow index testers can affect the accuracy and reliability of the measurements. These problems can include temperature inconsistencies, improper weight application, sample contamination, and user error. Pacorr’s MFI testers are designed to address these challenges with advanced features such as precise temperature control, accurate weight application mechanisms, and easy-to-clean components. Regular maintenance, calibration, and training are essential to ensure the accurate and reliable performance of the MFI tester.
Types of Melt Flow Index Testers
There are various types of melt flow index testers available, each designed to meet different levels of automation and user interaction. The main types of MFI testers include manual, semi-automatic, and fully automatic models. Each type offers distinct advantages and is suited for specific testing needs and operational environments.
Manual melt flow index testers are the most basic type and require significant operator involvement. These testers are typically more affordable and are suitable for laboratories with limited budgets or for applications where testing frequency is low. In a manual MFI tester, the operator is responsible for loading the sample, setting the temperature, applying the weight, and measuring the extruded polymer. While these testers require more hands-on operation, they are robust and reliable for straightforward testing scenarios. Pacorr’s manual MFI testers are designed to be user-friendly, with clear instructions and simple controls to facilitate accurate testing.
Semi-automatic melt flow index testers offer a higher level of automation compared to manual models. These testers automate some of the testing steps, such as temperature control and timing, reducing the potential for human error and increasing the repeatability of the tests. In a semi-automatic MFI tester, the operator still needs to load the sample and apply the weight, but the device handles the timing and measurement of the extruded polymer. This level of automation provides a good balance between cost and efficiency, making semi-automatic testers suitable for laboratories with moderate testing needs. Pacorr’s semi-automatic MFI testers are equipped with advanced features that enhance accuracy and ease of use.
Fully automatic melt flow index testers offer the highest level of automation, minimizing operator involvement and maximizing accuracy and repeatability. These testers automate all steps of the testing process, including sample loading, temperature control, weight application, timing, and measurement. Fully automatic MFI testers are ideal for high-throughput laboratories and industrial settings where testing frequency is high, and precision is critical. These testers provide consistent and reliable results with minimal operator intervention, reducing the risk of errors and improving testing efficiency. Pacorr’s fully automatic MFI testers are designed with state-of-the-art technology to deliver the highest level of performance and accuracy.
In addition to the level of automation, melt flow index testers can also vary based on specific features and capabilities. For example, some testers are designed to measure both melt flow rate (MFR) and melt volume rate (MVR), providing more comprehensive data on the polymer’s flow properties. Others may include advanced data logging and analysis features, allowing for detailed examination of test results. Pacorr offers a range of MFI testers with various features to meet diverse testing needs and industry requirements.
In conclusion, there are different types of melt flow index testers available, each suited for specific testing needs and operational environments. Manual, semi-automatic, and fully automatic models offer varying levels of automation and user interaction. Pacorr provides a comprehensive range of MFI testers, from basic manual models to advanced fully automatic systems, ensuring that users can find the right tester for their specific requirements. By choosing the appropriate type of MFI tester, manufacturers can ensure accurate and reliable measurement of the melt flow rate, optimizing their quality control processes and improving the performance of their products.
Melt Flow Index Test Standard
Melt flow index tests are conducted according to standardized methods to ensure consistency and comparability of results across different laboratories and testing scenarios. The two most commonly referenced standards for melt flow index testing are ASTM D1238 and ISO 1133. These standards specify the test conditions, including temperature, load, and sample preparation procedures, to ensure that the measurements are accurate and reliable.
ASTM D1238 is the standard test method for measuring the melt flow rates of thermoplastics by extrusion plastometer. This standard provides detailed guidelines on the apparatus, test conditions, and procedures to be followed for accurate measurement of the melt flow rate. It specifies the dimensions of the die, the weights to be used, and the temperatures for different types of polymers. Following ASTM D1238 ensures that the results are consistent and can be compared with those obtained in other laboratories using the same standard.
ISO 1133 is the international standard for determining the melt mass-flow rate (MFR) and melt volume-flow rate (MVR) of thermoplastics. Similar to ASTM D1238, ISO 1133 provides detailed guidelines on the test apparatus, conditions, and procedures. It specifies the requirements for the die, weights, and temperatures, ensuring that the measurements are accurate and reproducible. ISO 1133 also includes provisions for determining the melt density of the polymer, providing additional information on the material’s properties.
Both ASTM D1238 and ISO 1133 emphasize the importance of maintaining precise temperature control during the test. The temperature of the barrel must be controlled to within ±0.2°C of the specified temperature to ensure accurate measurement of the melt flow rate. The weights applied to the molten polymer must also be precise, with tolerances specified to ensure consistency in the applied load.
Pacorr’s melt flow index testers are designed to comply with both ASTM D1238 and ISO 1133 standards. These testers are equipped with advanced temperature control systems and accurate weight application mechanisms to ensure that the test conditions meet the required specifications. Pacorr provides detailed instructions and guidelines for conducting melt flow index tests according to these standards, helping users to achieve accurate and reliable results.
In addition to ensuring accuracy and reliability, following standardized test methods is essential for regulatory compliance and market acceptance. Many industries have stringent regulations regarding the properties of plastic materials, and compliance with these standards is necessary for market entry. By using a melt flow index tester that complies with ASTM D1238 and ISO 1133, manufacturers can ensure that their materials meet the required specifications and are accepted in the marketplace.
In conclusion, melt flow index tests are conducted according to standardized methods such as ASTM D1238 and ISO 1133 to ensure consistency and comparability of results. These standards specify the test conditions, including temperature, load, and sample preparation procedures, to ensure that the measurements are accurate and reliable. Pacorr’s MFI testers are designed to comply with these standards, providing accurate and reliable measurements that meet industry requirements. By following these standardized test methods, manufacturers can ensure the quality and performance of their plastic materials, facilitating regulatory compliance and market acceptance.
Melt Flow Index vs. Melt Volume Rate
Melt flow index (MFI) and melt volume rate (MVR) are two important parameters used to measure the flow properties of thermoplastic polymers. While they are related, they provide different information about the material’s behavior during processing. Understanding the distinction between these parameters is essential for interpreting test results and selecting appropriate materials for specific applications.
Melt flow index (MFI) measures the mass of polymer extruded through a die under specified conditions, typically expressed in grams per 10 minutes. It provides a measure of the material’s flowability or ease of flow when subjected to heat and pressure. A higher MFI indicates that the polymer has a lower viscosity and higher flowability, while a lower MFI indicates a higher viscosity and lower flowability. MFI is a widely used parameter in the plastic industry for quality control and material selection.
Melt volume rate (MVR), on the other hand, measures the volume of polymer extruded through a die under specified conditions, typically expressed in cubic centimeters per 10 minutes. MVR provides a measure of the material’s volumetric flow rate, which can be particularly useful for understanding the material’s behavior during processing, especially in applications where volumetric flow is critical. MVR is closely related to MFI, but it provides additional information on the material’s density and volumetric flow properties.
The relationship between MFI and MVR can be expressed by the equation: MVR = MFI / ρ, where ρ is the melt density of the polymer. This equation highlights the importance of melt density in interpreting MVR results. For materials with the same MFI, differences in melt density can lead to different MVR values. Understanding this relationship is essential for accurate material characterization and selection.
Pacorr’s melt flow index testers are capable of measuring both MFI and MVR, providing comprehensive data on the polymer’s flow properties. These testers are designed to comply with industry standards, such as ASTM D1238 and ISO 1133, ensuring that the measurements are accurate and reliable. Pacorr provides detailed guidelines and support for interpreting MFI and MVR results, helping users to make informed decisions based on the material’s flow characteristics.
When selecting materials for specific applications, it is important to consider both MFI and MVR. For instance, in injection molding processes, where precise control of material flow is essential, understanding the volumetric flow rate (MVR) can help optimize processing parameters and achieve better control over the molding process. In extrusion processes, where mass flow rate (MFI) is more critical, MFI can provide valuable insights into the material’s flow behavior and processing performance.
In conclusion, melt flow index (MFI) and melt volume rate (MVR) are two important parameters used to measure the flow properties of thermoplastic polymers. While MFI measures the mass of polymer extruded under specified conditions, MVR measures the volume of polymer extruded. Understanding the relationship between these parameters and the material’s melt density is essential for accurate material characterization and selection. Pacorr’s MFI testers are capable of measuring both MFI and MVR, providing comprehensive data on the polymer’s flow properties and helping users make informed decisions for their specific applications.
Buy Melt Flow Index Tester
When considering the purchase of a melt flow index tester, it is important to evaluate several key factors to ensure that the chosen device meets your specific testing needs and operational requirements. Factors such as accuracy, reliability, ease of use, compliance with industry standards, and after-sales support are critical in selecting the right MFI tester for your laboratory or manufacturing facility.
One of the primary considerations when buying a melt flow index tester is accuracy. The tester must provide precise and reliable measurements of the melt flow rate (MFR) to ensure that the results are consistent and comparable. Pacorr’s MFI testers are known for their high accuracy, featuring advanced temperature control systems and precise weight application mechanisms that ensure accurate measurement of the MFR. These testers are designed to comply with industry standards, such as ASTM D1238 and ISO 1133, ensuring that the results are reliable and consistent.
Reliability is another important factor to consider. The MFI tester should be robust and durable, capable of withstanding frequent use in a laboratory or industrial setting. Pacorr’s MFI testers are built with high-quality materials and components, ensuring long-term reliability and minimal maintenance requirements. These testers are designed to operate efficiently even under demanding conditions, providing consistent performance over time.
Ease of use is also a crucial consideration when selecting a melt flow index tester. The tester should be user-friendly, with intuitive controls and clear instructions that make it easy to operate. Pacorr’s MFI testers feature user-friendly interfaces and automated features that simplify the testing process, reducing the potential for human error and increasing the repeatability of the tests. These testers are designed to be easy to set up and operate, ensuring that users can quickly and accurately measure the melt flow rate of their materials.
Compliance with industry standards is essential for ensuring that the measurements obtained from the MFI tester are accurate and reliable. Pacorr’s MFI testers are designed to comply with ASTM D1238 and ISO 1133 standards, ensuring that the test conditions meet the required specifications. This compliance is crucial for regulatory compliance and market acceptance, ensuring that the materials tested meet the required standards and are accepted in the marketplace.
After-sales support is another important factor to consider when buying a melt flow index tester. It is important to choose a supplier that offers comprehensive support and services, including training, calibration, and maintenance. Pacorr provides extensive after-sales support, including detailed instructions and guidelines for operating and maintaining the MFI tester, as well as calibration services to ensure the accuracy and reliability of the device. This support helps users to operate the tester effectively and confidently, ensuring that they can achieve accurate and reliable results.
In conclusion, when buying a melt flow index tester, it is important to consider factors such as accuracy, reliability, ease of use, compliance with industry standards, and after-sales support. Pacorr’s MFI testers are known for their high accuracy, reliability, and user-friendly design, making them an excellent choice for laboratories and manufacturing facilities. With comprehensive support and services, Pacorr ensures that users can achieve accurate and reliable measurements, optimizing their quality control processes and improving the performance of their products.
Thanks to Pacorr Testing instruments, we have all the required quality testing instruments that have helped us to ensure the best quality delivered to our clients.
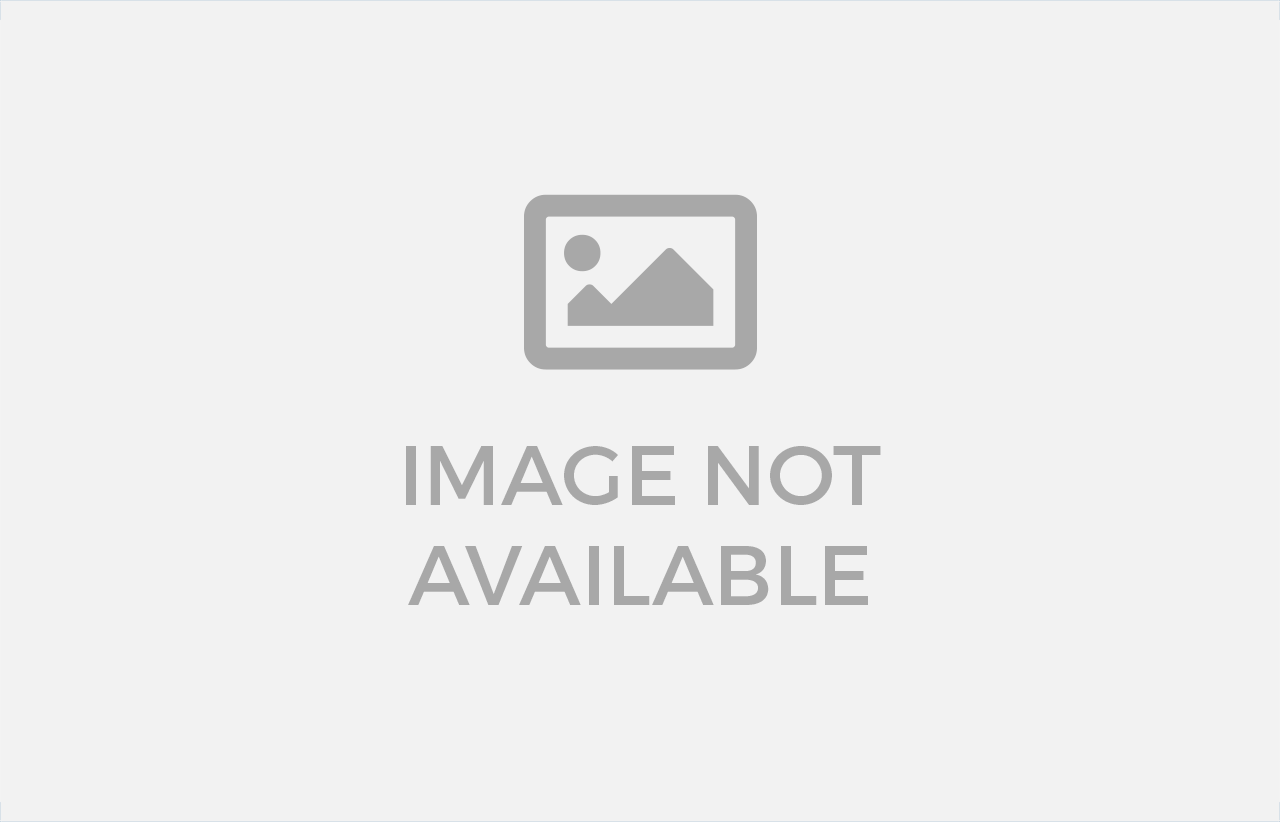
Danish
Fair Exports Pvt. Ltd.