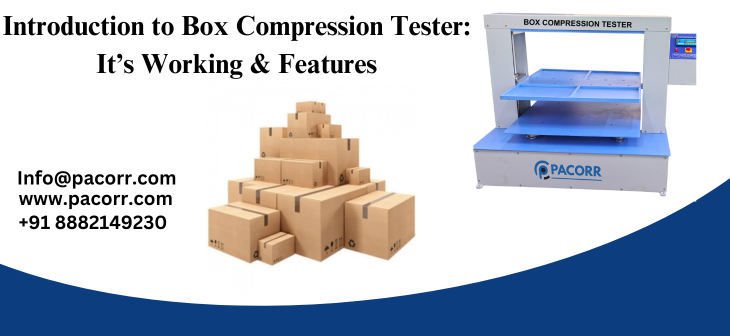
Ensuring the quality and durability of packaging materials is critical in various industries, especially for products that undergo long shipping processes. A box compression tester is an essential tool for assessing the strength and durability of boxes and other packaging materials. By simulating real-life conditions, this device helps manufacturers ensure that their packaging can withstand the rigors of transportation and storage. This article delves into the features, working principles, and importance of box compression testers, referencing industry standards such as ASTM D642, ASTM D4169, ISO 2234:2015, and EN ISO 12048.
Box Compression Tester: An Overview
A box compression tester is a machine designed to evaluate the compressive strength of packaging materials, such as boxes, cartons, and other containers. This testing apparatus is crucial for determining how much weight a box can endure before it deforms or fails. Industries use this data to enhance packaging designs, ensuring that products remain intact during handling, transportation, and storage.
Significance of Box Compression Testers in Packaging
Packaging materials are subjected to various stresses during their lifecycle. A robust box compression tester helps identify the maximum load a package can bear without getting damaged. This ensures that the contents within remain protected from potential hazards. Furthermore, maintaining packaging integrity helps in reducing costs associated with product damage and returns, thereby boosting customer satisfaction.
Working Principle of Box Compression Testers
The box compression tester operates on a straightforward principle: applying a compressive force on a test sample until it reaches its breaking point. Here is a detailed look at how these machines function:
- Sample Preparation: A box or container is placed on the lower platen of the tester.
- Force Application: The upper platen descends to apply a uniform compressive force on the sample.
- Data Recording: Sensors and load cells measure the force applied and the deformation of the sample.
- Analysis: The data collected is analyzed to determine the box’s maximum compressive strength.
This process helps manufacturers understand the performance limits of their packaging materials and make necessary adjustments to enhance durability.
Features of a Box Compression Tester
Modern box compression testers come equipped with a range of features designed to improve testing accuracy and efficiency:
- High Precision Load Cells: Ensure accurate measurement of compressive forces.
- Digital Display: Provides real-time data on force and deformation.
- Adjustable Platen Speed: Allows for varied testing speeds to simulate different conditions.
- Automatic Calibration: Enhances the precision and repeatability of tests.
- Safety Features: Includes overload protection and emergency stop functions.
These features collectively contribute to reliable and consistent testing outcomes, helping businesses maintain high-quality standards.
Standards Governing Box Compression Testing
Various international standards outline the procedures and specifications for box compression testing. Compliance with these standards ensures the credibility and reliability of test results. Key standards include:
- ASTM D642: This standard provides guidelines for determining the compressive resistance of shipping containers, components, and unit loads.
- ASTM D4169: Specifies performance testing procedures for shipping containers and systems, including environmental and dynamic tests.
- ISO 2234:2015: Outlines the method for vertical compression testing on complete, filled transport packages.
- EN ISO 12048: Defines compression and stacking tests for complete, filled transport packages.
Adhering to these standards helps manufacturers achieve uniformity in testing procedures, ensuring that packaging materials meet industry requirements.
Advantages of Using a Box Compression Tester
Investing in a box compression tester offers several benefits:
- Improved Product Safety: Ensures that packaging materials can protect contents during transit.
- Cost Savings: Reduces expenses associated with product damage and returns.
- Quality Assurance: Helps in maintaining high standards of packaging quality.
- Compliance: Assists in meeting regulatory and industry standards.
- Customer Satisfaction: Enhances the overall customer experience by delivering intact products.
By incorporating these devices into their quality control processes, manufacturers can significantly improve their packaging reliability and efficiency.
Applications of Box Compression Testers
Box compression testers find applications across various industries, including:
- Food and Beverage: Ensuring the packaging can withstand stacking in warehouses and transportation.
- Pharmaceuticals: Protecting sensitive products from damage during shipping.
- E-commerce: Maintaining package integrity through various stages of handling and delivery.
- Consumer Goods: Enhancing the durability of packaging for a wide range of products.
Each industry benefits from the precise testing capabilities of these machines, ensuring their packaging solutions are up to the mark.
Understanding Box Compression Test Results
Interpreting the results from a box compression test is crucial for improving packaging designs. The key parameters typically assessed include:
- Maximum Compression Strength: The highest force the box can withstand.
- Deformation at Peak Load: The extent of deformation before failure.
- Load-Deformation Curve: Illustrates the relationship between applied force and deformation.
These parameters provide valuable insights into the performance of packaging materials, guiding manufacturers in enhancing their designs for better durability and protection.
Technological Advancements in Box Compression Testers
With the rapid advancements in technology, modern box compression testers have become more sophisticated. Some of the latest innovations include:
- Automated Testing Systems: Enhance efficiency by reducing manual intervention.
- High-Resolution Sensors: Provide more accurate measurements.
- Data Integration: Allows for seamless data transfer and analysis using software tools.
- Remote Monitoring: Enables real-time monitoring and control of tests from remote locations.
These advancements not only improve the accuracy and reliability of tests but also streamline the overall testing process.
Pacorr’s Box Compression Tester
Pacorr, a leading provider of testing instruments, offers state-of-the-art box compression testers designed to meet the diverse needs of various industries. Their machines are known for their precision, durability, and user-friendly interfaces. Key features of Pacorr’s box compression testers include:
- Advanced Load Cells: For accurate force measurement.
- Robust Construction: Ensures long-lasting performance.
- User-Friendly Interface: Simplifies the testing process.
- Compliance with Standards: Meets ASTM D642, ASTM D4169, ISO 2234:2015, and EN ISO 12048 specifications.
Pacorr’s commitment to quality and innovation makes their box compression testers a reliable choice for businesses seeking to enhance their packaging quality.
Box Strength Testing: A Crucial Quality Control Measure
Box strength testing is an integral part of the quality control process in packaging. It involves subjecting boxes to various stress tests to evaluate their durability and resilience. The insights gained from these tests help manufacturers optimize their packaging designs, ensuring they meet the demands of different industries and applications.
Implementing Box Compression Testing in Quality Control
Incorporating box compression testing into quality control processes involves several steps:
- Defining Test Parameters: Based on industry standards and specific requirements.
- Selecting Test Samples: Representative samples from production batches.
- Conducting Tests: Using a box compression tester to apply compressive force.
- Analyzing Results: Interpreting data to identify areas for improvement.
- Adjusting Designs: Modifying packaging designs based on test outcomes.
This systematic approach helps in maintaining consistent packaging quality, reducing the risk of product damage during transit.
Challenges in Box Compression Testing
Despite its benefits, box compression testing can present certain challenges:
- Sample Variability: Differences in sample preparation can affect test results.
- Machine Calibration: Ensuring accurate calibration is critical for reliable results.
- Environmental Factors: Temperature and humidity can influence the performance of packaging materials.
Addressing these challenges requires meticulous planning and execution of testing procedures, as well as regular maintenance and calibration of testing equipment.
Future Trends in Box Compression Testing
The future of box compression testing is poised to witness several exciting trends:
- Integration with AI: Utilizing artificial intelligence for predictive analysis and optimization.
- Enhanced Automation: Increasing the use of automated systems for improved efficiency.
- Sustainable Testing Practices: Focusing on eco-friendly materials and processes.
- Global Standardization: Harmonizing testing standards across different regions.
These trends are set to revolutionize the way packaging materials are tested, ensuring higher standards of quality and sustainability.
What is a box compression tester?
A box compression tester is a device used to measure the compressive strength of packaging materials, such as boxes and cartons, by applying a uniform compressive force until the sample deforms or fails.
Why is box compression testing important?
Box compression testing is essential for ensuring that packaging materials can withstand the stresses of handling, transportation, and storage, thereby protecting the contents and reducing costs associated with product damage and returns.
What standards govern box compression testing?
Key standards include ASTM D642, ASTM D4169, ISO 2234:2015, and EN ISO 12048, which provide guidelines for testing procedures and specifications for compressive resistance of packaging materials.
How does a box compression tester work?
The tester applies a compressive force on a test sample placed between two platens. Sensors and load cells measure the force and deformation, and the data is analyzed to determine the box’s maximum compressive strength.
What features should I look for in a box compression tester?
Important features include high precision load cells, digital display, adjustable platen speed, automatic calibration, and safety features like overload protection and emergency stop functions.
What are the benefits of using a box compression tester?
Benefits include improved product safety, cost savings, quality assurance, compliance with standards, and enhanced customer satisfaction.
Conclusion
Box compression testing is a vital aspect of packaging quality control, ensuring that materials can endure the stresses of real-world conditions. With advancements in technology, modern box compression testers offer precise, reliable, and efficient testing solutions. Companies like Pacorr provide high-quality testers that meet international standards, helping businesses maintain high packaging standards and protect their products during transit.
In summary, the box compression tester plays a crucial role in safeguarding product integrity, optimizing packaging designs, and enhancing overall customer satisfaction. By adhering to established standards and leveraging the latest technological advancements, manufacturers can ensure their packaging solutions are robust and reliable.
Thanks to Pacorr Testing instruments, we have all the required quality testing instruments that have helped us to ensure the best quality delivered to our clients.
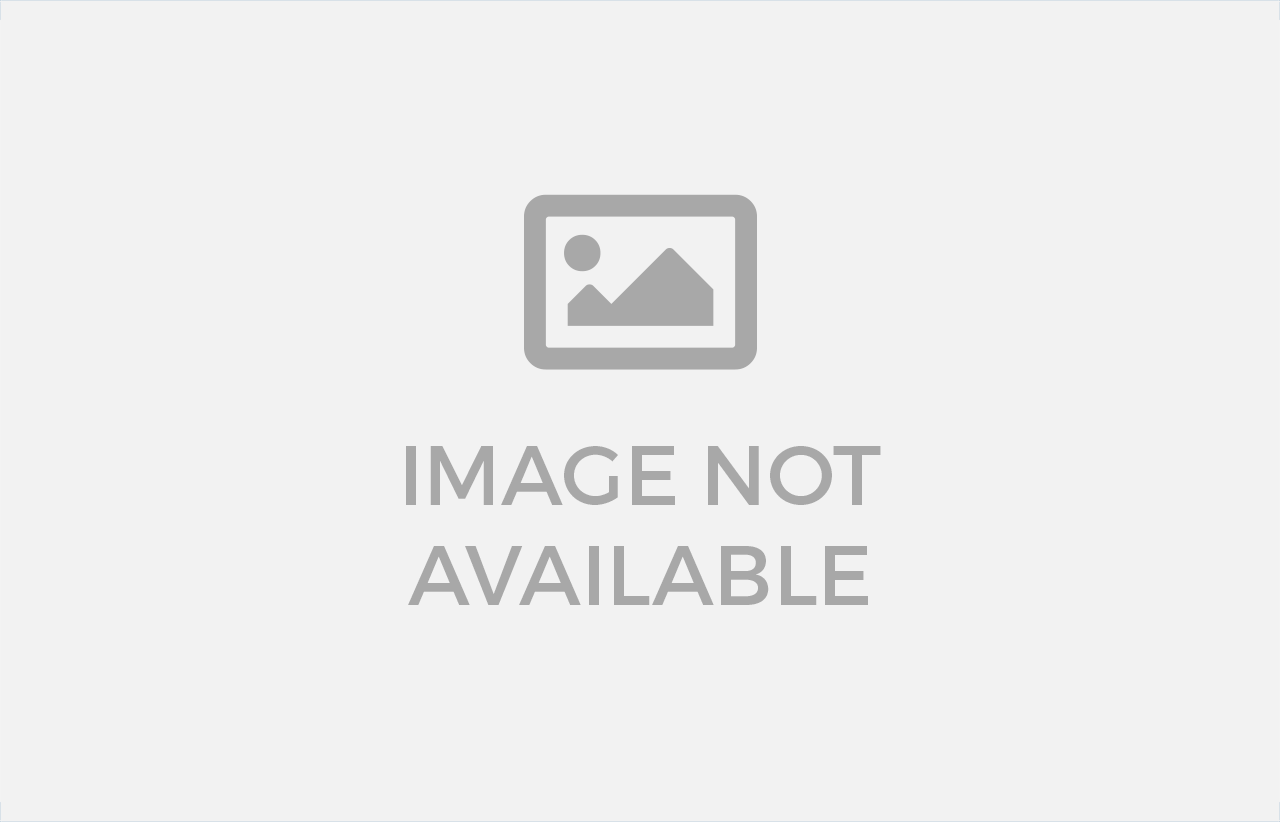
Danish
Fair Exports Pvt. Ltd.