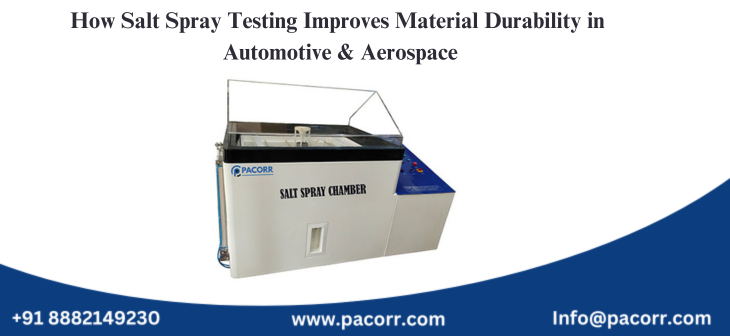
Corrosion is a persistent challenge across industries, leading to costly damage and structural failures. To combat this, salt spray testing plays a vital role in assessing the corrosion resistance of coatings, metals, and surface treatments. A salt spray chamber replicates harsh environmental conditions, allowing manufacturers to predict product longevity and ensure compliance with international standards such as ASTM B117, ISO 9227, JIS Z 2371, and ASTM G85. Companies like Pacorr provide advanced salt spray chambers, ensuring reliable and accurate corrosion testing across various industries.
What is a Salt Spray Chamber?
A salt spray chamber is a specialized testing apparatus designed to expose materials to a saline mist under controlled conditions. This accelerates the corrosion process, helping industries evaluate the effectiveness of protective coatings. The test is widely used in automotive, aerospace, marine, electronics, and construction sectors to ensure materials withstand real-world environments.
How the Salt Spray Chamber Works
- Salt Solution Preparation – A 5% sodium chloride (NaCl) solution is prepared using distilled water to create a controlled corrosive environment.
- Atomization & Fogging – Pressurized air disperses the solution into the chamber, forming a fine mist.
- Exposure Duration – Samples remain in the chamber for hours or days, depending on testing standards.
- Evaluation – Post-test, samples are assessed for signs of corrosion, including rust, pitting, or coating degradation.
- Compliance Check – Results are compared against industry benchmarks to determine if the material meets durability standards.
ASTM B117: The Most Common Salt Spray Test
The ASTM B117 standard is the most widely adopted guideline for neutral salt spray (NSS) testing. It sets strict conditions for solution preparation, exposure settings, and assessment methods, ensuring consistent and repeatable results.
Key ASTM B117 Testing Conditions:
- Salt Solution: 5% NaCl with a pH of 6.5 to 7.2.
- Temperature: Maintained at 35°C (95°F) inside the chamber.
- Fog Collection Rate: 1.0–2.0 ml per hour per 80 cm² of exposed surface.
- Test Duration: Varies by industry, ranging from 24 to 96 hours or more.
- Evaluation: Examines pitting, coating breakdown, and general material failure.
- ISO 9227: International Corrosion Testing Standard
The ISO 9227 standard defines various salt spray test types, each tailored for specific corrosion conditions:
- Neutral Salt Spray (NSS) – Uses a 5% NaCl solution (similar to ASTM B117).
- Acetic Acid Salt Spray (AASS) – Incorporates acetic acid for a more aggressive test.
- Copper-Accelerated Acetic Acid Salt Spray (CASS) – Further intensifies corrosion with copper ions.
ISO 9227 Highlights:
- Consistent solution and pH control for reliable results.
- Maintains 35°C temperature for neutral salt spray tests.
- Used in automotive, marine, and aerospace industries.
JIS Z 2371: Japan’s Corrosion Testing Standard
The JIS Z 2371 standard aligns with global benchmarks but includes additional parameters tailored to Japan’s industrial needs.
JIS Z 2371 Testing Specifications:
- Salt Solution: Identical to ASTM and ISO standards.
- Temperature: Maintained at 35°C.
- Test Duration: Ranges from 24 to 1000 hours based on material type.
- Evaluation Method: Uses visual inspection and weight loss measurements to assess corrosion resistance.
- Industry Use: Common in automotive, electronics, and marine sectors.
- ASTM G85: Advanced Corrosion Testing for Extreme Conditions
ASTM G85 builds upon ASTM B117 by introducing modified salt spray tests that simulate harsher environments. These test methods include:
- Prohesion Testing (Annex A1): Alternates between salt fog exposure and drying cycles.
- Acidified Salt Fog Test (Annex A2): Introduces sulfur dioxide (SO₂) to replicate industrial pollution effects.
- Dilute Electrolyte Cyclic Fog/Dry Test (Annex A3): Mimics marine exposure conditions.
- Seawater Acidified Test (Annex A4): Used for offshore and marine structures.
- SO₂ Contaminated Salt Fog Test (Annex A5): Simulates extreme atmospheric conditions.
Why ASTM G85 is Important:
- Provides realistic environmental simulations for demanding applications.
- Essential for long-term corrosion resistance validation.
- Enhances traditional salt spray testing with cyclic variations.
Industries Benefiting from Salt Spray Testing
Salt spray chambers are critical in various sectors where material durability is a priority:
- Automotive: Ensures corrosion-resistant body panels, fasteners, and coatings.
- Aerospace: Tests aircraft components exposed to high humidity and saline conditions.
- Marine: Evaluates ship hulls, offshore platforms, and marine coatings.
- Electronics & Electrical Components: Ensures circuit boards and metal enclosures withstand corrosion.
- Construction & Infrastructure: Assesses protective coatings on steel structures, bridges, and pipelines.
Choosing the Right Salt Spray Chamber
When selecting a salt spray chamber, Pacorr recommends considering:
- Standard Compliance: Ensure compatibility with ASTM B117, ISO 9227, JIS Z 2371, or ASTM G85.
- Chamber Size: Choose a model that accommodates the required test sample volume.
- Automation & Controls: Look for advanced programmable cycles, real-time monitoring, and data logging features.
- Durability & Maintenance: Opt for chambers with corrosion-resistant materials like fiberglass-reinforced plastics.
Salt spray testing is a critical tool for evaluating material durability, ensuring compliance with international standards, and improving product longevity. Companies like Pacorr offer high-performance salt spray chambers, helping industries enhance corrosion resistance and minimize failures. By following rigorous testing protocols, manufacturers can develop stronger, longer-lasting products while meeting regulatory requirements.
For industries that prioritize corrosion resistance, adopting standardized salt spray testing is an essential step toward delivering high-quality, durable products.
Thanks to Pacorr Testing instruments, we have all the required quality testing instruments that have helped us to ensure the best quality delivered to our clients.
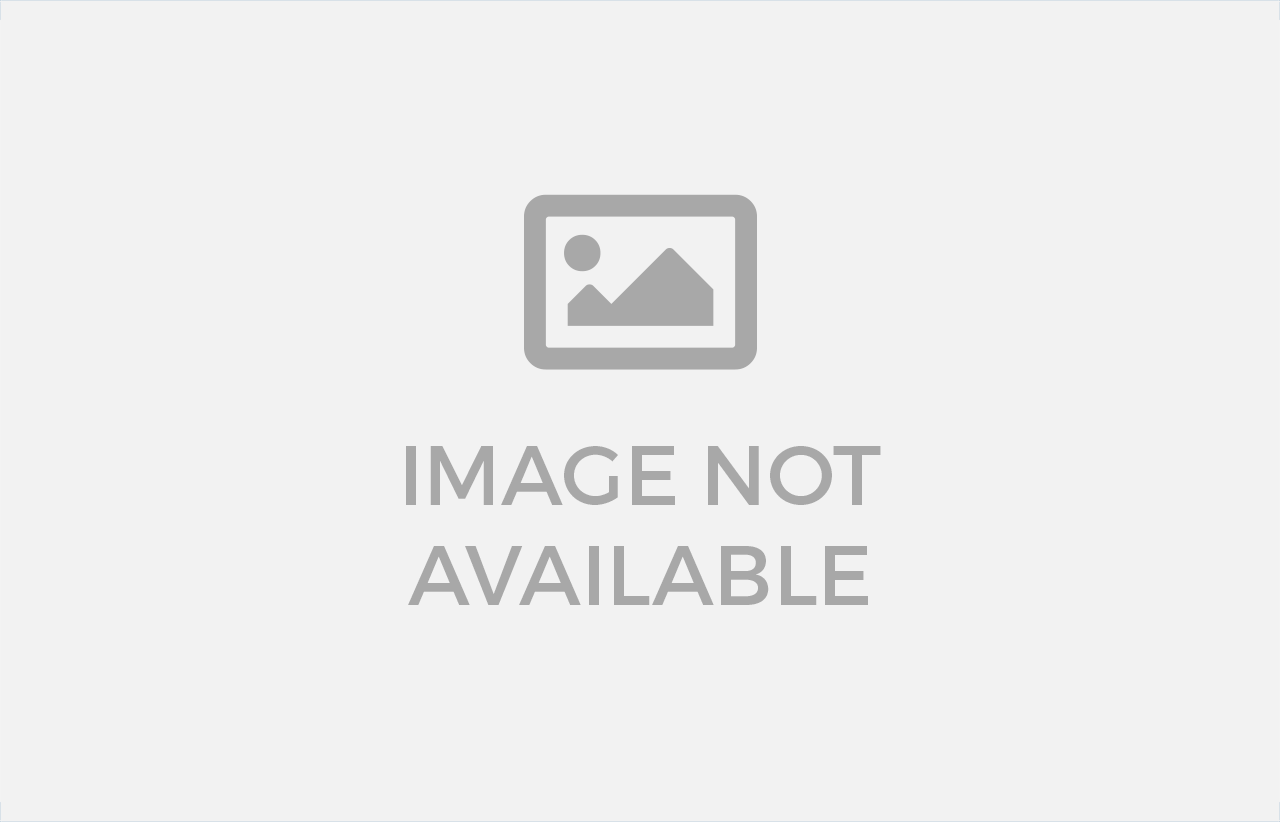
Danish
Fair Exports Pvt. Ltd.