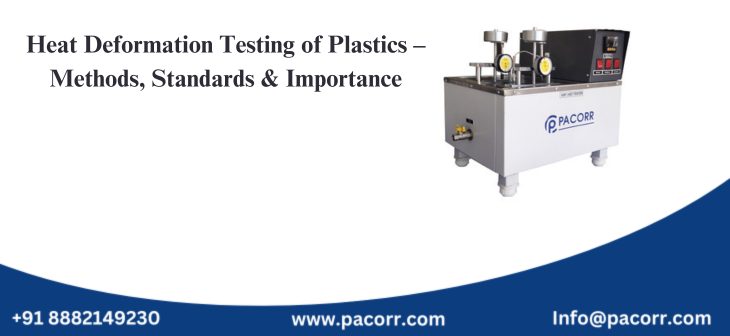
Plastics have become indispensable in modern industries, replacing traditional materials like metals and ceramics due to their lightweight, cost-effectiveness, and ease of processing. However, one major concern with plastic materials is their thermal stability—their ability to retain shape and strength when exposed to high temperatures.
Understanding heat deformation is essential for industries such as automotive, aerospace, electronics, medical devices, and packaging, where plastics are frequently subjected to elevated temperatures. Heat deformation testing helps manufacturers determine the temperature limits of plastics and assess their heat resistance under load.
This article delves deep into heat deformation testing methods, industry standards like ASTM D648 and ASTM D1525, and the importance of polymer heat resistance testing. It also covers the thermal properties of plastics and how different factors influence plastic deformation at high temperatures.
What is Heat Deformation Testing?
Heat deformation testing is a scientific method used to evaluate how plastic materials behave when subjected to high temperatures and mechanical stress. It helps manufacturers determine whether a polymer can withstand thermal expansion, softening, or distortion when exposed to real-world conditions.
Why is Heat Deformation Testing Important?
- Ensures material reliability in high-temperature applications.
- Helps industries comply with quality and safety standards.
- Prevents structural failures in products exposed to heat.
- Aids in the selection of heat-resistant polymers.
By conducting heat resistance measurement for plastics, industries can ensure product durability and compliance with international standards.
Types of Heat Deformation Tests for Plastics
1. Heat Deflection Temperature (HDT) Testing
The Heat Deflection Temperature (HDT) test measures the temperature at which a plastic specimen deforms under a specific mechanical load.
Testing Procedure
- A standardized plastic sample is placed under a fixed bending load.
- The sample is heated at a controlled rate.
- The temperature at which the sample deflects by a predetermined amount is recorded as the HDT value.
Key Benefits of HDT Testing
- Determines the maximum service temperature of plastics.
- Essential for automotive, aerospace, and industrial applications.
- Ensures compliance with ASTM D648, the international standard for HDT measurement.
2. Vicat Softening Point (VSP) Testing
The Vicat Softening Point (VSP) test measures the temperature at which a plastic material begins to soften under a specified force.
Testing Process
- A needle-like probe is pressed against the sample with a constant force.
- The sample is gradually heated at a standardized rate.
- The temperature at which the probe penetrates a set depth is recorded as the VSP value.
Importance of VSP Testing
- Determines a polymer’s softening temperature before reaching its melting point.
- Ensures compliance with ASTM D1525, the industry standard for Vicat softening point measurement.
- Used in industries that require materials with precise thermal performance, such as medical devices and food packaging.
Thermal Analysis of Polymers
Thermal analysis helps manufacturers understand how plastics react to temperature changes, including melting, expansion, and degradation.
Key Thermal Analysis Techniques
- Differential Scanning Calorimetry (DSC) – Measures heat flow to identify melting points and phase transitions.
- Thermogravimetric Analysis (TGA) – Evaluates thermal stability by measuring weight loss under heat exposure.
- Dynamic Mechanical Analysis (DMA) – Assesses viscoelastic behavior of plastics at varying temperatures.
These techniques are essential for selecting heat-resistant plastics and optimizing polymer formulations.
Factors Affecting Plastic Deformation Under Heat
1. Polymer Structure
- Amorphous Polymers (e.g., ABS, polycarbonate) soften gradually.
- Semi-Crystalline Polymers (e.g., polyethylene, nylon) have a sharp melting point.
2. Environmental Conditions
- UV Exposure can accelerate polymer degradation.
- Humidity and Oxygen Levels affect material heat stability.
3. Processing Conditions
- Cooling rates during molding impact heat resistance.
- Filler materials and additives enhance thermal performance.
ASTM Standards for Heat Resistance Testing
ASTM D648 – HDT Compliance Tester
ASTM D648 provides guidelines for heat deflection temperature (HDT) testing. It helps manufacturers determine a material’s ability to withstand thermal stress under load.
ASTM D1525 – VSP Compliance Tester
ASTM D1525 ensures accurate measurement of Vicat softening temperature, an important parameter for polymer selection and material validation.
How to Choose the Right Heat Deformation Testing Equipment?
Selecting the right testing instrument is essential for accurate heat resistance evaluation.
1. Compliance with Industry Standards
- Choose a Heat Deflection Temperature Tester that complies with ASTM D648 and an ASTM D1525 Compliance Tester for Vicat Softening Point testing.
2. Accuracy and Precision
- Look for instruments with high-resolution sensors.
- Consider automated data logging for better accuracy.
3. Multi-Function Testing Capability
- A dual-function HDT/VSP Tester offers comprehensive heat resistance analysis.
Future Trends in Thermal Testing of Polymers
1. AI-Powered Testing
- Automated AI-driven testing methods enhance accuracy and predict material failure under thermal stress.
2. Sustainable Heat-Resistant Polymers
- Research is advancing eco-friendly, heat-resistant plastics to replace traditional petroleum-based polymers.
3. Non-Destructive Testing (NDT) Methods
- Emerging infrared thermography and ultrasonic techniques provide real-time thermal analysis without damaging materials.
Heat deformation testing is crucial for assessing plastic performance under elevated temperatures. By using HDT/VSP testers, thermal analysis techniques, and ASTM compliance methods, manufacturers can ensure material reliability and durability.
Investing in advanced heat resistance measurement ensures plastics meet quality standards, preventing product failures in high-temperature applications.
Frequently Asked Questions (FAQs)
1. What is the difference between HDT and VSP?
HDT measures deformation under load, while VSP identifies softening temperature under a specified force.
2. Why is ASTM D648 important?
It sets the standard for HDT testing, ensuring quality and compliance.
3. How does heat resistance testing benefit manufacturers?
It prevents product failures and ensures thermal stability.
4. Can recycled plastics undergo heat testing?
Yes, testing ensures recycled polymers maintain thermal performance.
5. What industries rely on heat deformation testing?
Automotive, aerospace, electronics, and packaging sectors.
Thanks to Pacorr Testing instruments, we have all the required quality testing instruments that have helped us to ensure the best quality delivered to our clients.
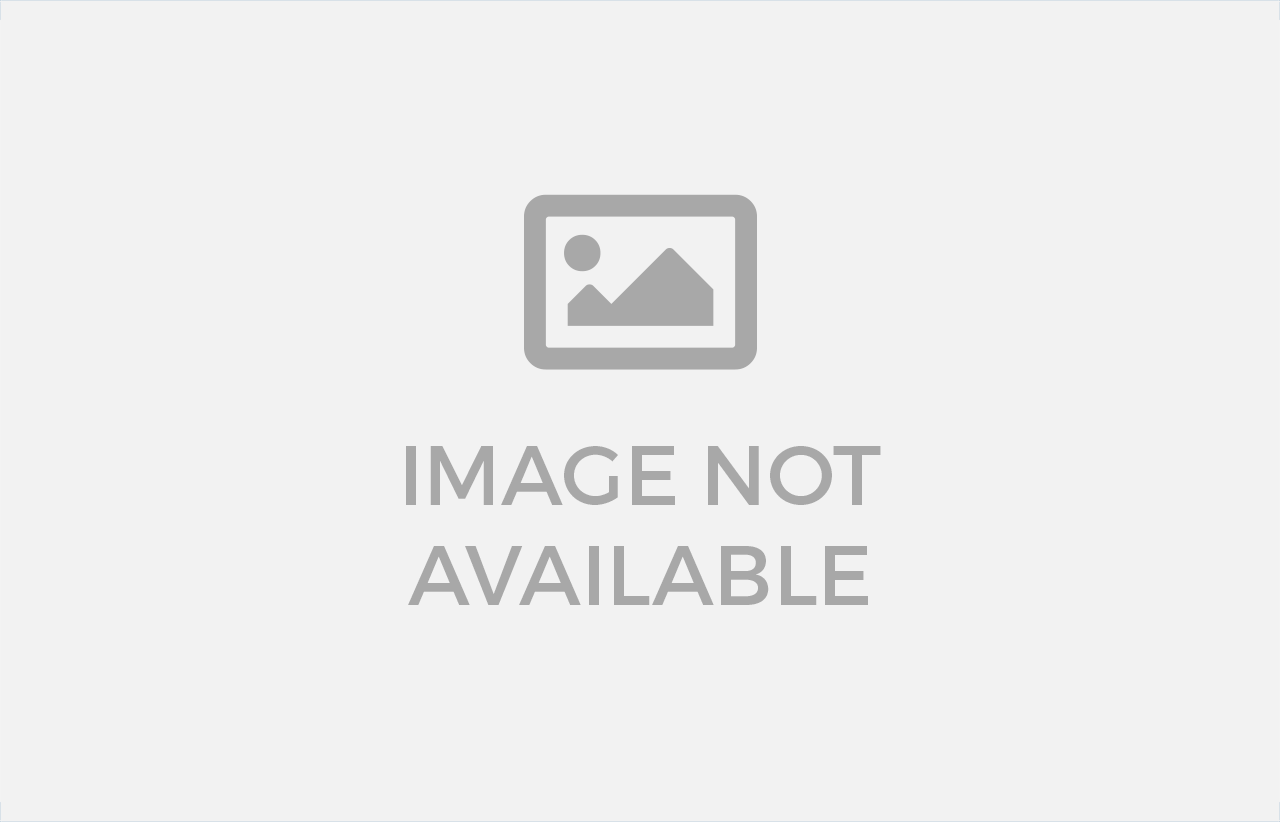
Danish
Fair Exports Pvt. Ltd.