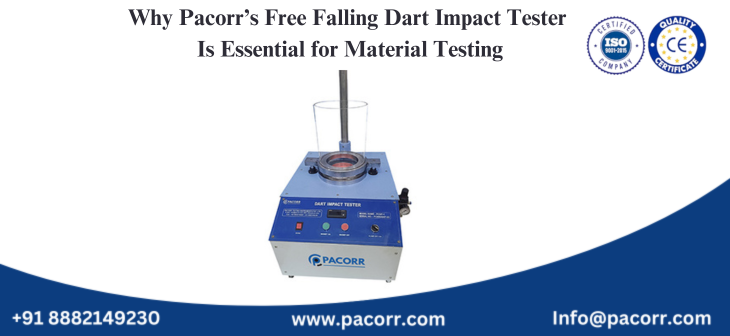
Pacorr's Free Falling Dart Impact Tester is essential in today's highly competitive industrial environment, where ensuring product durability and reliability is paramount. This advanced testing instrument is crucial for maintaining stringent quality control, particularly in industries working with plastics and films. Manufacturers rely heavily on Pacorr's tester to assess the toughness and impact resistance of materials accurately. This guide provides an in-depth exploration of the Pacorr's Free Falling Dart Impact Tester, detailing its operational principles, applications, benefits, and relevant international standards.
What is a Pacorr's Free Falling Dart Impact Tester?
The Pacorr's Free Falling Dart Impact Tester is a sophisticated apparatus specifically designed to measure the resistance of plastic films, sheets, and packaging materials against impact by a free-falling dart. It simulates real-world scenarios where materials might encounter sudden impacts, allowing manufacturers to understand how materials behave under stress. By quantifying impact resistance, businesses can ensure that their products meet both industry requirements and consumer expectations.
Working Principle of the Pacorr's Free Falling Dart Impact Tester
The testing process involves dropping a weighted dart from a specified height onto the sample material. The dart is designed with a specific shape and weight to replicate typical impacts that packaging might experience during handling, transportation, or accidental drops. The tester measures whether the material punctures or withstands the impact. Typically, the test continues with varying weights until a clear failure or resistance threshold is established.
Why Manufacturers Trust Pacorr for Dart Impact Resistance Testing
Key Components
- Weighted Dart: A standardized dart with adjustable weights.
- Sample Holder: Securely holds the material in place.
- Drop Height Adjustment: Enables precise control of dart drop height.
- Impact Surface: A flat, smooth area where the sample is positioned for testing.
- Automated Release Mechanism: Ensures consistency and repeatability of test results.
Importance of Dart Impact Testing
In sectors such as packaging, automotive, construction, and consumer goods, understanding impact resistance helps manufacturers produce superior products that resist damage during practical use. It contributes significantly to reducing product returns, enhancing customer satisfaction, and maintaining brand reputation.
- Industries Benefiting from Dart Impact Testing
- Packaging: Ensuring packaging materials withstand transportation and handling impacts.
- Plastics Manufacturing: Assessing durability for films, sheets, and molded parts.
- Automotive Sector: Verifying plastic components' strength and resilience.
- Medical Supplies: Guaranteeing safety and integrity of medical packaging.
Benefits of Using a Pacorr's Free Falling Dart Impact Tester
Accurate and Reliable Results
This tester delivers precise, consistent measurements, allowing manufacturers to reliably assess material properties. By following standardized testing procedures, businesses can confidently produce products with predictable performance.
Enhanced Product Durability
Identifying weaknesses early helps companies improve their manufacturing processes, ensuring end products are robust and resilient to common impacts encountered during their lifecycle.
Cost Savings
Reducing product failures directly translates to lower costs related to product returns, warranty claims, and waste from damaged goods. Investing in robust testing protocols ultimately boosts profitability.
Compliance with International Standards
Using a Pacorr's Free Falling Dart Impact Tester ensures compliance with global quality standards, significantly easing international trade and expanding market reach.
How to Conduct a Dart Impact Test?
Sample Preparation
Before testing, ensure samples are cut to standard sizes. Condition samples according to industry standards (typically ASTM or ISO), maintaining consistent environmental conditions such as temperature and humidity.
Testing Procedure
- Secure the sample firmly in the testing area.
- Set the dart to the required weight and height based on the testing standard.
- Activate the release mechanism to drop the dart onto the sample.
- Inspect the sample for puncture or damage.
- Repeat tests with varying weights until establishing a consistent failure threshold.
Analysis and Interpretation
Results typically yield values that help determine the impact resistance properties. The energy absorbed by the material before puncture provides crucial insights into its toughness and reliability under real-world conditions.
Relevant Standards Associated with Dart Impact Testing
Complying with international standards ensures that tests are consistent, reliable, and globally recognized. Below are key standards commonly associated with dart impact testing:
- ASTM D1709: Standard test methods for impact resistance of plastic films by free-falling dart method.
- ISO 7765-1: Specifies test methods for determining the impact resistance of plastic films using a free-falling dart.
- ISO 7765-2: Specifically deals with instrumented puncture test methods.
- JIS K 7124: Japanese standard for impact resistance testing of plastic films and sheets.
Advanced Features to Consider in a Dart Impact Tester
Digital Display and Control
Modern testers include digital displays and automated control systems that improve ease of use, reduce operator errors, and enhance accuracy and repeatability.
Automated Data Recording
Built-in data management systems streamline data collection, storage, and analysis, significantly reducing manual documentation efforts and ensuring accuracy and traceability.
Adjustable Height and Dart Weight Systems
Adjustable components enable versatile testing conditions, accommodating a wide variety of materials and testing requirements according to international standards.
Safety Features
Modern testers include safety shields, automatic lockout systems, and emergency stop features, ensuring operator safety during tests.
Revolutionizing Quality Control: The Dart Impact Tester
Maintenance and Calibration of the Pacorr's Free Falling Dart Impact Tester
Regular calibration and maintenance are critical for ensuring test accuracy. Manufacturers should routinely calibrate equipment according to industry guidelines, verifying weight accuracy, dart height precision, and overall mechanical integrity. Preventive maintenance schedules prolong the equipment’s operational lifespan, optimize performance, and maintain compliance with testing standards.
Common Challenges and Solutions
Variability in Results
Variations can occur due to inconsistent sample preparation or environmental conditions. Ensuring uniform sample conditions and adhering strictly to standardized methods significantly reduce variability.
Equipment Wear and Tear
Regular inspections and timely replacement of worn components prevent inaccuracies. Maintaining a detailed log of maintenance activities helps track equipment health.
Investing in a Pacorr's Free Falling Dart Impact Tester is indispensable for manufacturers aiming to deliver high-quality, impact-resistant products. By understanding the working principles, adhering to international standards, and utilizing advanced features of these testers, businesses can significantly enhance product reliability, reduce operational costs, and ensure compliance. As the market demands durable and reliable materials, using advanced testing instruments like the Pacorr's Free Falling Dart Impact Tester becomes a necessity rather than a choice, positioning manufacturers as leaders in quality assurance and innovation.
Thanks to Pacorr Testing instruments, we have all the required quality testing instruments that have helped us to ensure the best quality delivered to our clients.
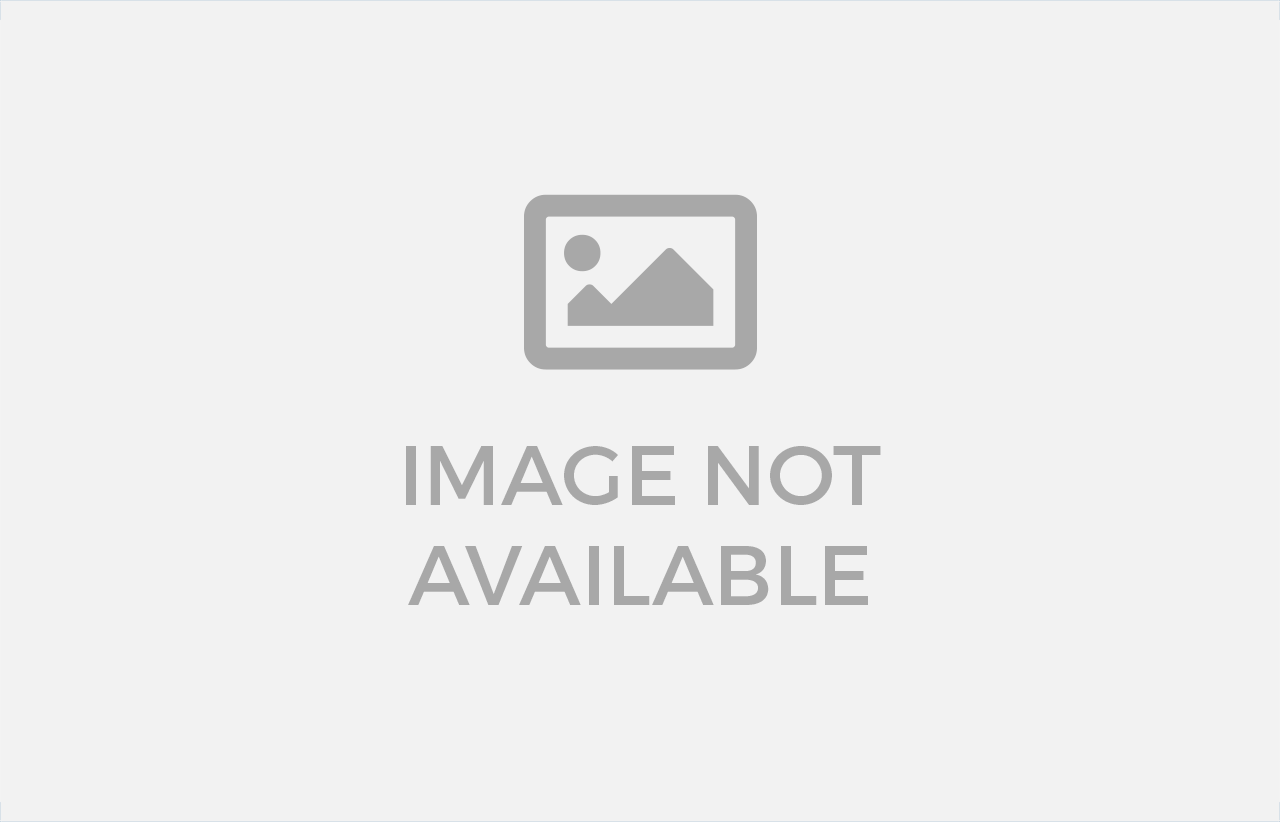
Danish
Fair Exports Pvt. Ltd.