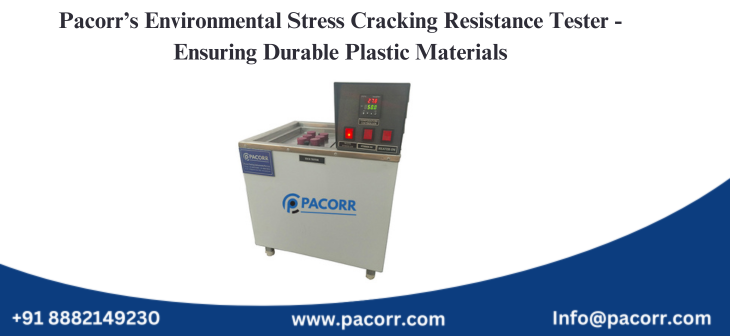
Plastic materials are widely used in various industries due to their versatility, durability, and cost-effectiveness. However, one of the biggest challenges faced by plastic manufacturers is Environmental Stress Cracking (ESC) a phenomenon that leads to premature material failure when plastics are exposed to mechanical stress and chemical agents. This can cause structural damage, leaks, and product malfunctions, making it essential to test plastic components for their resistance to environmental stress cracking.
To evaluate the durability and reliability of plastic materials, the Environmental Stress Cracking Resistance (ESCR) Tester, following the ASTM D1693-15 standard, is widely used. This test method provides a controlled laboratory assessment, helping manufacturers determine the ability of plastic materials especially polyethylene to withstand environmental stress and chemical exposure over time.
This article explores Environmental Stress Cracking (ESC), ASTM D1693-15 testing standards, the working mechanism of the ESCR Tester, its applications, benefits, and why it is a crucial testing instrument for quality control.
What is Environmental Stress Cracking (ESC)?
Environmental Stress Cracking (ESC) is a failure mechanism in plastic materials caused by the combined effect of mechanical stress and environmental exposure. Unlike direct chemical degradation, which results in the breakdown of polymer chains, ESC occurs when external stress and chemical exposure lead to microscopic cracks that gradually expand and cause material failure.
Key Factors Contributing to ESC:
- Chemical Exposure: Contact with oils, detergents, cleaning agents, fuels, and industrial chemicals weakens plastic structure.
- Mechanical Stress: Constant bending, stretching, or pressure creates internal strain, making plastics more vulnerable to cracking.
- Temperature Fluctuations: Changes in environmental temperature can impact plastic flexibility and strength, accelerating stress cracking.
- Material Composition: Certain plastics, such as polyethylene (PE) and polystyrene (PS), are more susceptible to ESC.
- Manufacturing Defects: Improper molding, extrusion, and residual stresses during production can make plastics prone to cracking.
Why is ESC a Critical Concern?
Environmental stress cracking can lead to serious product failures in industries such as packaging, automotive, construction, medical devices, and consumer goods. If plastic products are not tested for stress-cracking resistance, they may develop cracks under real-world conditions, resulting in safety hazards, increased maintenance costs, and product recalls.
To prevent such failures, manufacturers use the Environmental Stress Cracking Resistance Tester, which determines whether a material can withstand environmental stress and remain functional over time.
ASTM D1693-15: Standard Test Method for ESCR Testing
The ASTM D1693-15 test method is an internationally recognized quality control standard for evaluating the resistance of polyethylene plastics to environmental stress cracking. This test helps manufacturers ensure that their materials meet the required durability standards and do not fail under mechanical and chemical stress.
Key Features of ASTM D1693-15 Testing:
- Standardized sample preparation for accurate and repeatable results.
- Controlled chemical exposure to accelerate stress cracking.
- Precise application of mechanical stress under defined conditions.
- Time-based crack observation and analysis for material evaluation.
The ESCR test is critical for quality assurance, as it helps manufacturers determine whether a plastic formulation is suitable for specific applications and if it can withstand real-world conditions.
How Does the Environmental Stress Cracking Resistance Tester Work?
The Environmental Stress Cracking Resistance (ESCR) Tester is designed to simulate real-world stress conditions to evaluate the durability and resistance of plastic materials. The test involves a step-by-step process, ensuring accuracy and consistency in results.
Step-by-Step ESCR Testing Process:
1. Sample Preparation:
- Standard plastic specimens are cut from the material being tested.
- Notches are introduced at specific points to create stress concentration areas.
2. Chemical Exposure:
- The test specimens are immersed in a chemical agent (such as a surfactant or detergent) to accelerate crack formation.
- The concentration and type of chemical solution vary based on the material being tested.
3. Application of Stress:
- The samples are placed in a bending fixture, applying mechanical stress at a controlled angle.
- A temperature-controlled environment ensures test consistency.
4. Observation and Crack Evaluation:
- The samples are monitored at regular intervals for crack initiation and propagation.
- The time taken for visible cracks to appear is recorded and analyzed.
- The results determine the plastic material’s resistance to environmental stress cracking.
By conducting this test, manufacturers can ensure that plastic materials meet durability and safety standards, preventing failures in real-world applications.
Industries That Require ESCR Testing
The Environmental Stress Cracking Resistance Tester is widely used across various industries to improve product performance and reliability.
1. Packaging Industry
- Ensures plastic bottles, containers, and packaging films can withstand transportation, storage, and chemical exposure.
- Prevents leakage, contamination, and product failure.
2. Automotive Sector
- Tests fuel tanks, coolant reservoirs, and under-the-hood plastic parts for resistance to mechanical stress and exposure to automotive fluids.
- Enhances vehicle safety and durability.
3. Medical and Healthcare
- Evaluates medical device casings, syringes, and pharmaceutical containers for resistance to sterilization chemicals and stress.
- Ensures patient safety and product longevity.
4. Construction and Infrastructure
- Assesses plastic pipes, fittings, and insulation materials for resistance to mechanical pressure and environmental exposure.
- Ensures structural stability and long-term performance.
5. Consumer Goods
- Tests plastic furniture, storage containers, and household appliances to ensure resistance to wear and tear.
- Improves product lifespan and user experience.
Why Choose Pacorr’s ESCR Tester?
Pacorr offers high-precision Environmental Stress Cracking Resistance Testers designed for accurate and reliable testing of plastic materials. Our advanced testing solutions help manufacturers meet quality standards and industry regulations, ensuring that their products remain durable and defect-free.
Key Benefits of Using an ESCR Tester:
- Enhances Product Quality: Ensures that plastic materials can withstand real-world stress conditions.
- Reduces Product Failures: Prevents material cracking and structural damage.
- Ensures Compliance: Meets ASTM D1693-15 and industry-specific standards.
- Optimizes Material Selection: Helps manufacturers choose the best plastic formulations.
The Environmental Stress Cracking Resistance Tester (ASTM D1693-15) is an essential instrument for testing the durability of plastic materials. Industries such as packaging, automotive, construction, and healthcare rely on ESCR testing to ensure that their products are safe, reliable, and long-lasting.
For advanced testing instruments, trust Pacorr your partner in precision-engineered quality testing solutions.
Thanks to Pacorr Testing instruments, we have all the required quality testing instruments that have helped us to ensure the best quality delivered to our clients.
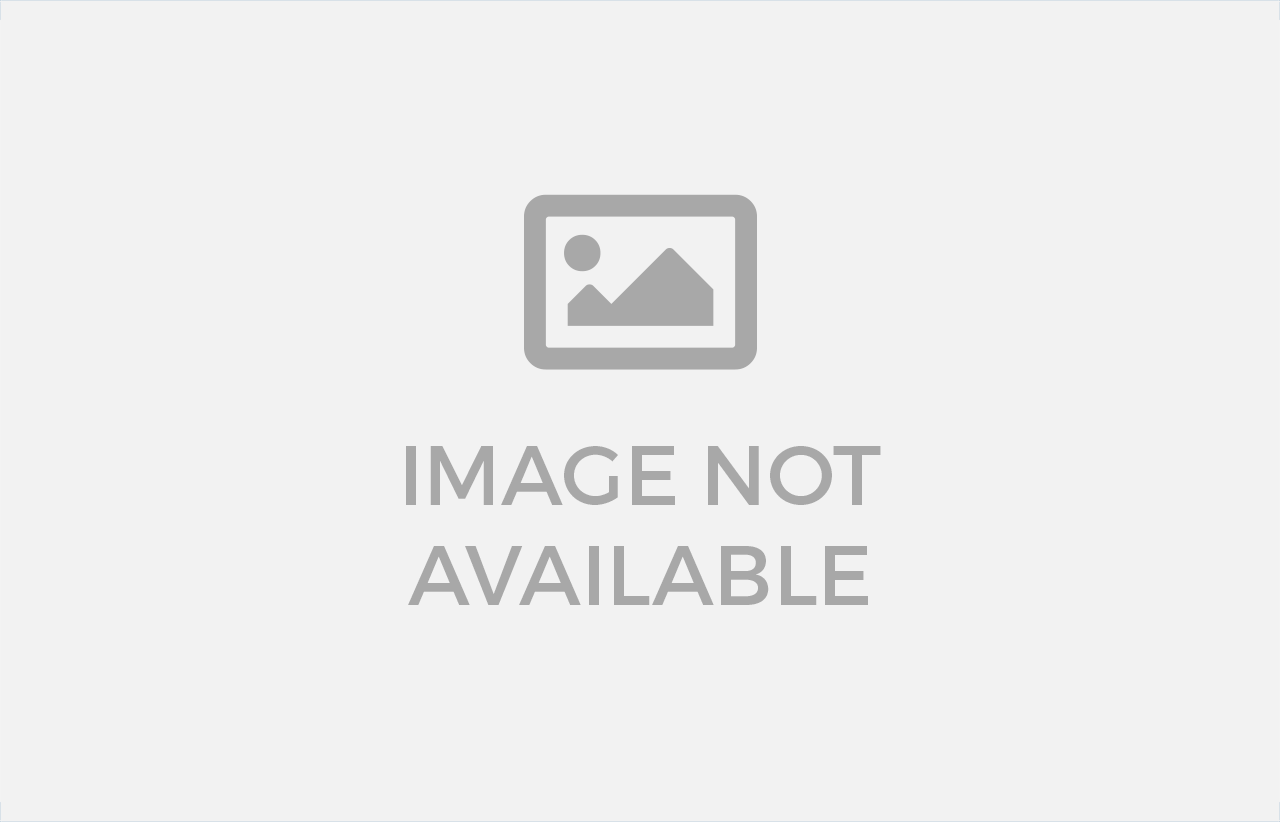
Danish
Fair Exports Pvt. Ltd.