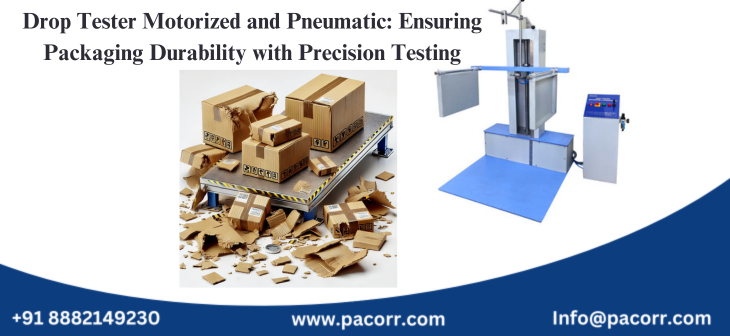
Drop Tester (Motorized and Pneumatic) is an advanced testing instrument designed to assess packaging strength and impact resistance by simulating real-world transportation and handling conditions. In the field of packaging and material testing, ensuring product integrity is essential, whether for delicate electronics or heavy industrial components. By conducting precise drop tests, this equipment helps manufacturers verify that packaging meets quality and safety standards, minimizing the risk of damage before products reach consumers.
This article will delve into the importance of drop testing, the functionality of motorized and pneumatic drop testers, their key benefits, industry applications, and essential factors to consider when selecting the right model for your testing requirements.
Understanding Drop Testing and Its Importance
Drop testing is a standardized method used across industries to determine how well a package or product can withstand free-fall impacts during transportation, storage, and handling. It assesses parameters such as shock absorption, structural integrity, and damage thresholds under controlled conditions.
Why Is Drop Testing Essential?
- Ensures Product Safety – Protects fragile and sensitive products from breakage during shipping.
- Regulatory Compliance – Meets international testing standards like ASTM D5276, ISO 2248, and ISTA.
- Cost Reduction – Helps manufacturers design cost-effective yet durable packaging.
- Quality Assurance – Enhances brand reputation by preventing defects and customer complaints.
By conducting systematic drop tests, manufacturers can identify weak points in packaging and optimize designs for better durability and performance.
Motorized vs. Pneumatic Drop Testers: Key Differences and Functionality
Drop testers come in different configurations, with motorized and pneumatic models being the most advanced and widely used variants.
Motorized Drop Tester
A motorized drop tester features an electromechanical lifting mechanism that allows precise control over the drop height and release mechanism. It is ideal for testing a variety of products, from small consumer goods to large industrial items.
Features & Benefits:
- Adjustable Drop Height – Ensures repeatable and controlled drop testing.
- Versatile Testing Capability – Suitable for different product sizes and weights.
- Enhanced Accuracy – Minimizes variations in drop angles and impact forces.
- User-Friendly Interface – Simple operation with digital controls.
Pneumatic Drop Tester
A pneumatic drop tester utilizes compressed air to release the sample instantly, ensuring a perfect free-fall without additional force or bias. It is commonly used for precision testing in industries requiring high accuracy.
Features & Benefits:
- Faster Drop Execution – Eliminates mechanical resistance for natural free-fall motion.
- Higher Load Capacity – Handles heavier products with improved efficiency.
- Ideal for Fragile Items – Prevents pre-impact vibrations that could affect test accuracy.
Both models offer unmatched reliability for drop testing applications, making them essential for R&D laboratories, quality control departments, and packaging manufacturers.
Industries That Rely on Drop Testing
Several industries depend on drop testing to ensure product durability and packaging efficiency:
1. E-Commerce & Retail
With the rise of online shopping, proper packaging testing is crucial to prevent damage during shipping and handling.
2. Electronics & Consumer Goods
Smartphones, laptops, and other delicate gadgets require drop testing to withstand accidental falls.
3. Pharmaceuticals & Medical Devices
Medical equipment must remain intact and sterile during transport, making drop testing essential.
4. Automotive & Aerospace
Component packaging must endure extreme conditions, ensuring parts remain secure and undamaged.
5. Food & Beverage
Bottle packaging, particularly for glass containers, undergoes drop testing to reduce breakage risks.
Each industry benefits from advanced drop testing methods to guarantee safe and reliable product delivery.
Choosing the Right Drop Tester: Factors to Consider
Selecting the ideal motorized or pneumatic drop tester depends on several factors:
- Product Type & Weight – Lighter items may require a motorized model, while heavier loads benefit from pneumatic testers.
- Drop Height Requirements – Adjustable height settings provide versatile testing conditions.
- Testing Standards Compliance – Ensure the tester adheres to ASTM, ISTA, and ISO standards.
- Ease of Operation – A user-friendly control panel and automated functions enhance efficiency.
- Customization Options – Some models offer custom drop angles and fixtures for specialized applications.
By evaluating these factors, manufacturers can invest in a drop tester that best suits their testing needs and operational workflow.
Investing in Advanced Drop Testing Solutions
A Drop Tester (Motorized and Pneumatic) is an indispensable tool for businesses focused on product safety, quality control, and regulatory compliance. By accurately simulating real-world impacts, these testers help manufacturers enhance packaging performance, minimize damages, and reduce costs.
Whether in electronics, pharmaceuticals, automotive, or e-commerce, implementing a reliable drop testing process ensures that products reach consumers in perfect condition. Investing in the right drop tester guarantees long-term quality assurance and brand credibility.
Thanks to Pacorr Testing instruments, we have all the required quality testing instruments that have helped us to ensure the best quality delivered to our clients.
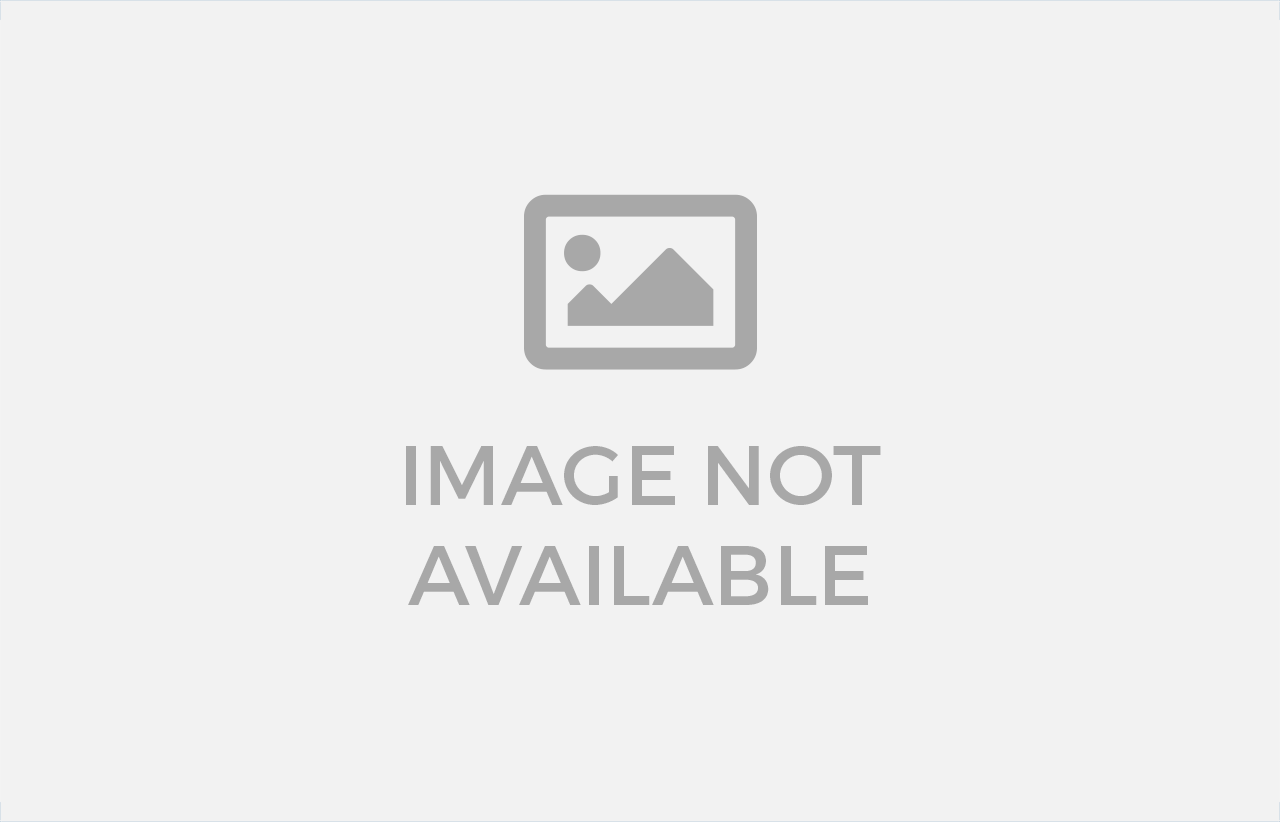
Danish
Fair Exports Pvt. Ltd.