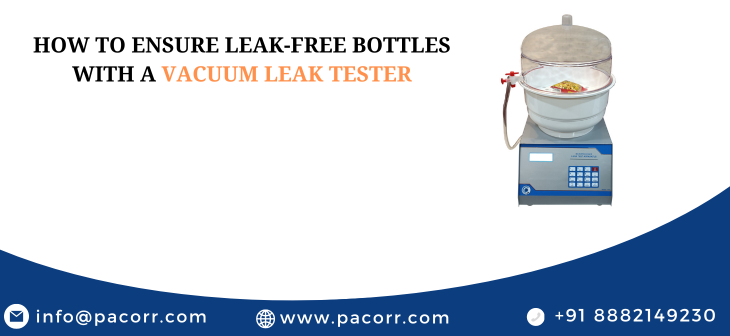
A single leak can compromise the quality and safety of a product, leading to customer dissatisfaction, potential recalls, and financial losses. The solution lies in advanced quality control methods that ensure every product reaches consumers in optimal condition. Among these methods, the vacuum leak tester stands out as an indispensable tool. In this guide, we will delve deep into how to ensure leak-free bottles using a vacuum leak tester and discuss the standards set forth by ASTM D6653. We will also highlight the unique features and benefits of Pacorr's vacuum leak tester, an industry-leading solution for quality assurance.
Understanding the Importance of Leak Testing in Packaging
Leak testing plays a crucial role in ensuring the integrity of packaged products, particularly in industries like food and beverage, pharmaceuticals, and cosmetics. A compromised seal can lead to:
- Contamination: Ingestible products may become exposed to bacteria, chemicals, or other contaminants.
- Product Loss: Liquids may leak out, resulting in a reduction of the product's weight or volume.
- Customer Complaints: Leaking bottles lead to unsatisfied customers and potential brand damage.
- Financial Impact: Replacing defective products or recalling entire batches can result in significant costs.
Therefore, leak testing is a vital quality control process. It's not just about maintaining product quality but also about meeting regulatory standards and preserving brand reputation.
What Is a Vacuum Leak Tester?
A vacuum leak tester, also known as a vacuum leakage tester, is a device used to detect leaks in packaging, particularly in bottles, pouches, and containers. The principle behind its operation involves creating a vacuum inside a chamber containing the test specimen. If there are leaks in the packaging, air or fluid will escape into the vacuum, causing visible bubbles or a drop in the vacuum level.
How Does a Vacuum Leak Tester Work?
- Sample Preparation: The test sample (bottle, pouch, etc.) is placed in a chamber filled with water or another suitable liquid.
- Vacuum Application: The chamber is sealed, and a vacuum is created inside. This reduces the pressure around the test sample.
- Leak Detection: If the packaging has any leaks, air will escape from the bottle into the water, forming visible bubbles. The presence of bubbles indicates a leak.
ASTM D6653 Standard for Vacuum Leak Testing
ASTM D6653 is a standard test method for determining the susceptibility of packages to leak under vacuum. It provides guidelines for evaluating the integrity of packages, particularly those intended for air shipment. Key points include:
- Scope: The standard covers the procedure for leak detection using a vacuum chamber.
- Significance and Use: It is particularly relevant for packages subjected to low atmospheric pressures, such as those transported via air.
- Procedure:
- The test package is placed in a vacuum chamber with a specified amount of water or suitable liquid.
- A vacuum is created and held for a specific duration.
- Leaks are detected by observing the presence of bubbles.
Ensuring Leak-Free Bottles with Pacorr's Vacuum Leak Tester
Pacorr, a leading manufacturer and supplier of quality testing instruments, offers an advanced vacuum leak tester that complies with ASTM D6653 standards. Here's how it can help ensure leak-free bottles:
Features of Pacorr's Vacuum Leak Tester
- Digital Control Panel: Allows precise control of vacuum levels and testing time.
- Durable Construction: The device is built with high-quality materials for prolonged use.
- Transparent Chamber: Enables clear observation of the test sample during the vacuum process.
- Variable Vacuum Levels: Allows the user to adjust vacuum levels to simulate different transport conditions.
- Pressure Indicator: Offers real-time monitoring of the vacuum pressure inside the chamber.
Benefits of Using Pacorr's Vacuum Leak Tester
- Accurate Leak Detection: Provides precise results, helping manufacturers identify defective packaging quickly.
- Compliance with Standards: Meets ASTM D6653 requirements, ensuring packaging integrity even for air shipment.
- User-Friendly Operation: Easy-to-use controls and clear observation features simplify the testing process.
- Versatile Applications: Suitable for testing various packaging types, including bottles, pouches, and containers.
- Reduced Waste: Early detection of leaks reduces the need for costly recalls and product wastage.
How to Use Pacorr's Vacuum Leak Tester
- Prepare the Chamber: Fill the vacuum chamber with water or another suitable liquid up to the indicated level.
- Place the Test Sample: Position the test sample inside the chamber, ensuring it is fully submerged.
- Seal the Chamber: Close the chamber lid to create an airtight seal.
- Set Test Parameters: Using the digital control panel, set the vacuum level and testing duration according to the package specifications.
- Start the Test: Activate the vacuum pump to create the desired vacuum inside the chamber.
- Observe for Leaks: Watch for bubbles around the test sample during the vacuum phase. If bubbles are present, the sample has a leak.
- Analyze Results: Record the results and compare them against the acceptable limits.
Applications of Pacorr's Vacuum Leak Tester
The versatility of Pacorr's vacuum leak tester makes it suitable for various industries:
- Food and Beverage: Ensures leak-free bottles and pouches for juices, sauces, and other consumables.
- Pharmaceuticals: Detects leaks in medicinal bottles and blister packs to prevent contamination.
- Cosmetics: Confirms the integrity of cosmetic containers, maintaining product quality.
- Industrial Chemicals: Identifies leaks in chemical packaging to avoid hazardous spills.
Best Practices for Leak Testing with a Vacuum Leak Tester
To maximize the efficiency of your leak testing process:
- Choose Appropriate Vacuum Levels: Different packaging materials may require varying vacuum levels. Test and adjust accordingly.
- Ensure Proper Submersion: The test sample should be fully submerged in the liquid for accurate results.
- Regular Calibration: Periodically calibrate the vacuum leak tester to maintain its accuracy.
- Monitor Testing Conditions: Ensure consistent temperature and pressure conditions to avoid external factors influencing results.
- Document Results: Keep detailed records of each test for quality control and regulatory compliance purposes.
Conclusion
Ensuring leak-free bottles is essential for maintaining product quality, safety, and brand reputation. A vacuum leak tester, particularly Pacorr's ASTM D6653-compliant model, offers an accurate, reliable, and efficient solution for leak detection. By following best practices and leveraging Pacorr's advanced features, manufacturers can detect leaks early, minimize wastage, and guarantee customer satisfaction.
What People Say
Thanks to Pacorr Testing instruments, we have all the required quality testing instruments that have helped us to ensure the best quality delivered to our clients.
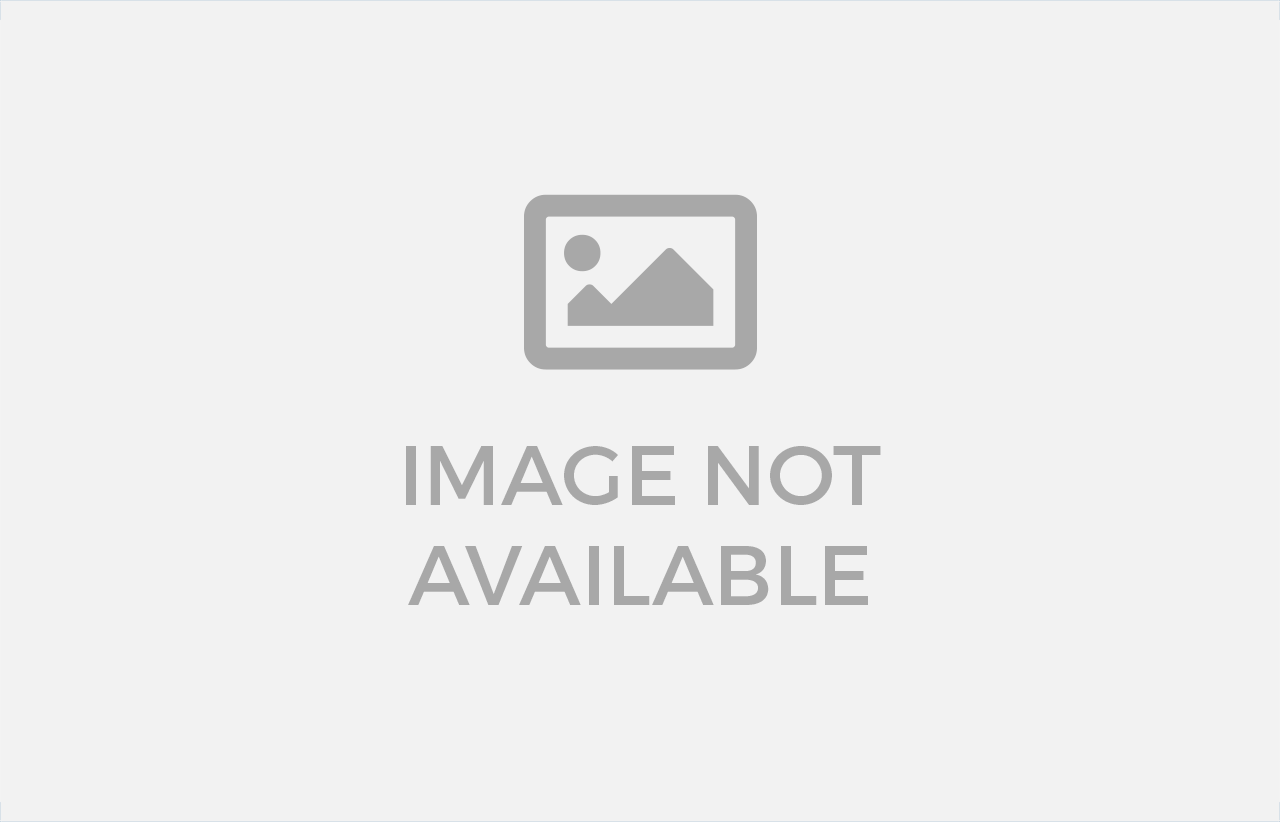
Danish
Fair Exports Pvt. Ltd.