
The durability of packaging is an important factor that determines how well the packaging can protect the product during transportation, handling, and storage. Here are some ways to check the durability of packagings:
- Compression Testing: This test involves applying a compressive load to the packaging to measure its resistance to compression. The test can be conducted using a compression tester, which applies a specific amount of force to the packaging, and the deformation of the packaging is measured.
- Drop Testing: This test is used to measure the packaging's ability to withstand impacts and shocks during handling and transportation. The packaging is dropped from a specific height, and the impact is measured using an accelerometer.
- Vibration Testing: This test is used to simulate the effects of transportation on the packaging. The packaging is subjected to vibration, and the impact of the vibration on the packaging is measured.
- Temperature and Humidity Testing: This test is used to determine the packaging's ability to withstand different environmental conditions. The packaging is subjected to various temperature and humidity conditions to assess its performance under different conditions.
- Permeability Testing: This test is used to measure the packaging's ability to prevent the ingress of moisture, gasses, and other contaminants. The packaging is placed in a controlled environment, and the rate of permeation of gasses and moisture is measured.
- Accelerated Aging Testing: This test is used to simulate the effects of aging on the packaging. The packaging is exposed to elevated temperatures, humidity, and light to accelerate the aging process, and the packaging's performance is measured.
By conducting these tests, manufacturers can evaluate the durability of the packaging and identify any potential weaknesses. This information can be used to improve the packaging design and ensure that the packaging provides adequate protection to the product.
How does a drop tester work?
A drop tester/drop testing machine is a type of packaging testing equipment that is used to simulate the impact of drops and shocks that can occur during transportation and handling. Here's how a drop tester works:
Step 1 - Preparation: The first step is to prepare the packaging for testing. The packaging is typically filled with a product or material that simulates the weight and dimensions of the actual product.
Step 2 - Setup: The packaging is placed on the drop tester, which typically consists of a platform with a mechanism for raising and dropping the packaging.
Step 3 - Test Parameters: The test parameters are set, including the drop height and the number of drops. The drop height is determined based on the type of product and the expected handling and transportation conditions.
Step 4 - Drop Test: The drop impact tester is activated, and the packaging is dropped from the specified height. The impact of the drop is measured using sensors that detect the acceleration, deceleration, and duration of the impact.
Step 5 - Analysis: The data collected during the drop test is analyzed to determine the packaging's performance. The packaging is inspected for damage, and any defects or weaknesses are identified.
Step 6 - Report: A report is generated that includes the test parameters, the results of the test, and any recommendations for improving the packaging design.
By using a drop tester, manufacturers can evaluate the performance of their packaging and identify any potential weaknesses. This information can be used to improve the packaging design and ensure that the product is adequately protected during transportation and handling. To know more about drop impact testers, contact Pacorr Testing Instruments.
Thanks to Pacorr Testing instruments, we have all the required quality testing instruments that have helped us to ensure the best quality delivered to our clients.
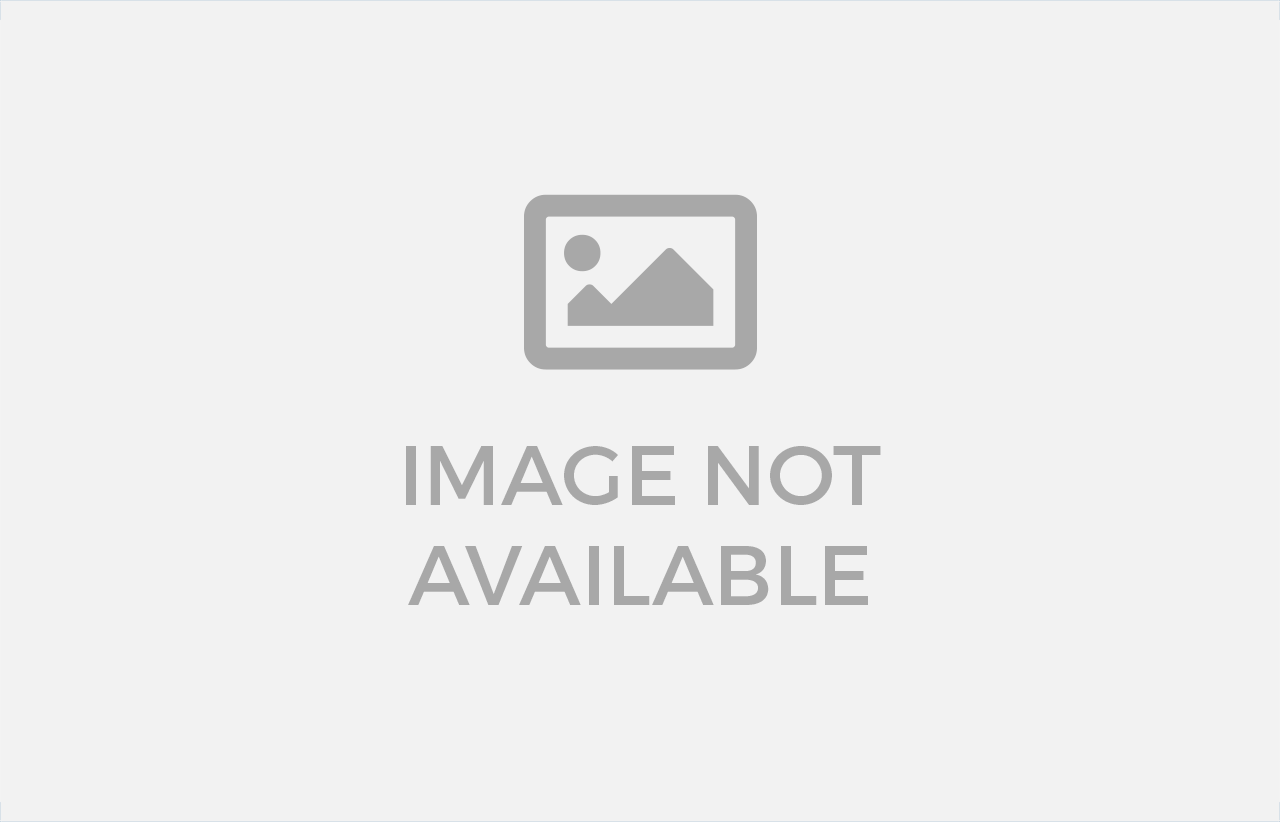
Danish
Fair Exports Pvt. Ltd.