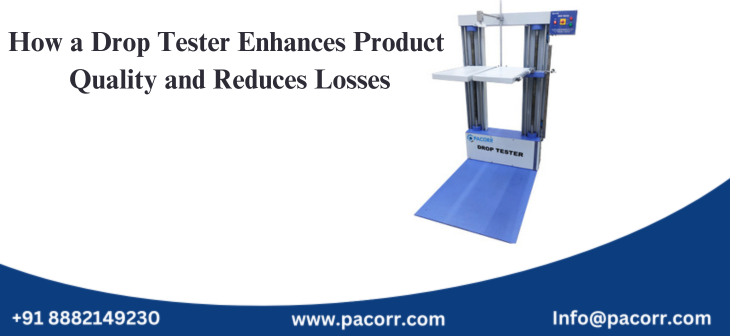
A drop tester is an essential tool in today’s competitive manufacturing industry, where ensuring product quality and durability is critical for customer satisfaction and safeguarding your brand’s reputation. Packaging integrity, a key factor in the process, ensures your goods are safely transported and stored. By simulating real-world conditions, a drop tester plays a pivotal role in maintaining quality standards. But what makes this instrument so indispensable, and why should it become a cornerstone of your manufacturing process? Let’s explore its importance.
The Role of a Drop Tester in Quality Assurance
A drop tester is designed to simulate the free-fall conditions that your product or its packaging might encounter during handling, transit, or storage. By replicating real-world scenarios, it provides valuable insights into how well your product can withstand accidental drops, vibrations, and impacts.
Key Applications of Drop Testing:
- Packaging Durability: Validates that your packaging can withstand physical shocks.
- Product Robustness: Evaluates the strength and durability of your product.
- Supply Chain Simulation: Mimics the conditions your product faces during transit.
- Standards Compliance: Ensures adherence to industry and international durability standards.
With the data collected from drop testing, you can refine your materials, designs, and structural elements, ensuring optimal product and packaging quality.
Benefits of Using a Drop Tester in Your Manufacturing Unit
1. Ensures Packaging Safety
Your packaging is designed to protect your product during transportation, but poor materials or flawed designs can lead to breakage and financial losses. A drop tester helps you identify vulnerabilities in your packaging, ensuring it meets safety standards and minimizes damage risks.
2. Enhances Product Durability
Drop testing evaluates not only the packaging but also the product itself. Whether you produce electronics, glassware, or machinery, understanding how your product responds to impact helps you refine its design and materials, improving its durability.
3. Reduces Costly Returns and Replacements
Damaged goods are a leading cause of customer dissatisfaction and returns. By testing and strengthening your product and packaging proactively, you can reduce damage during transit, saving money and protecting your bottom line.
4. Strengthens Brand Reputation
Delivering intact, high-quality products builds customer trust and satisfaction. A drop tester ensures that only the best versions of your product reach your customers, setting your brand apart from competitors.
5. Facilitates Industry Compliance
Many industries require strict adherence to packaging and durability standards. A drop tester provides reliable data to meet these requirements, ensuring legal compliance and earning trust from stakeholders.
6. Promotes Sustainability
By identifying weak points in your packaging, you can reduce excess material usage without compromising protection. This contributes to global sustainability goals and appeals to environmentally conscious customers.
Key Features of a Modern Drop Tester
When choosing a drop tester, consider the following features to ensure its value:
- Adjustable Drop Heights: Simulates various conditions based on real-world scenarios.
- Customizable Fixtures: Adapts to different product sizes and shapes.
- Precision Controls: Provides accurate drop angles and repeatable results.
- Durability: Withstands frequent, long-term testing cycles.
- Standards Compliance: Meets benchmarks such as ASTM, ISO, and ISTA.
Investing in a durable, feature-rich drop tester ensures efficient and reliable testing tailored to your manufacturing requirements.
Why You Should Invest in a Drop Tester
The benefits and features of a drop tester make it a vital investment for your manufacturing process. Here’s why:
- Cost Efficiency: While a drop tester requires an initial investment, it reduces long-term losses from damaged goods, returns, and material waste.
- In-House Testing: Owning a drop tester gives you the flexibility to test as often as needed, refining your designs and packaging without delays.
- Quality Control: Ensures consistent product quality, increasing customer satisfaction and reducing recalls.
- Faster Time-to-Market: Streamlined testing accelerates the production process, giving you a competitive edge.
- Versatility: Applicable to various industries, including FMCG, electronics, pharmaceuticals, and e-commerce.
Conclusion
A drop tester is more than just a quality assurance tool—it’s an investment in your product’s success and your brand’s reputation. By simulating real-world conditions, it provides actionable insights that help improve durability, minimize losses, and enhance customer satisfaction. For a manufacturer seeking to stay competitive, a drop tester is an essential asset for achieving quality, compliance, and sustainability.
To ensure precision and long-term value, choose a trusted solution like Pacorr’s drop testers. Designed for reliability and tailored to meet your specific needs, a Pacorr drop tester can elevate your manufacturing processes and ensure your product’s excellence in the marketplace.
Thanks to Pacorr Testing instruments, we have all the required quality testing instruments that have helped us to ensure the best quality delivered to our clients.
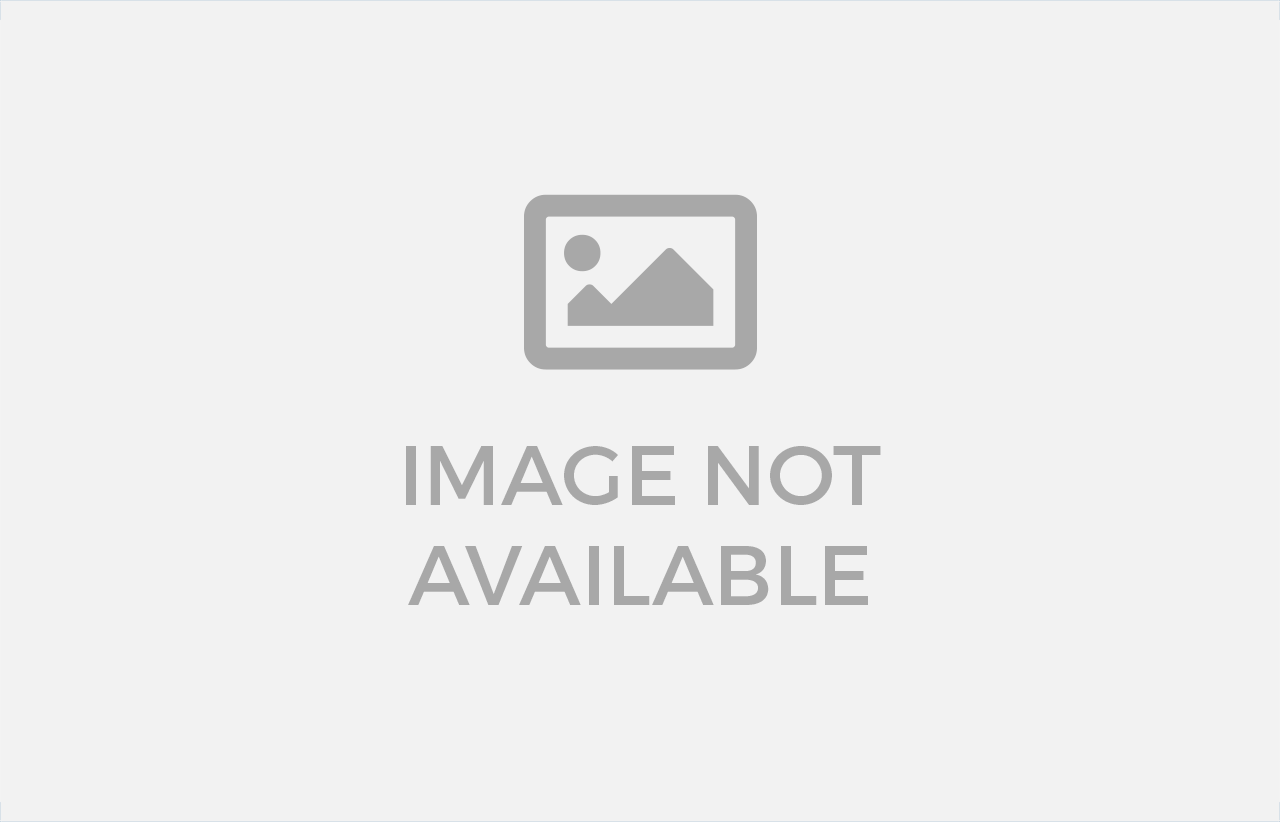
Danish
Fair Exports Pvt. Ltd.