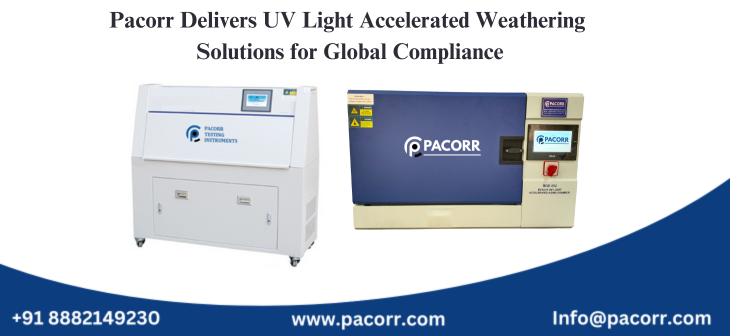
UV Weathering Test Chamber is the tool I trust when it comes to replicating long-term environmental damage in a controlled and accelerated setting. At Pacorr, I’ve seen how crucial this testing is for ensuring material reliability, especially in an era where failure simply isn’t an option. Sunlight, moisture, and fluctuating temperatures can silently degrade plastics, coatings, polymers, and automotive components often without warning. That’s why environmental testing plays such a central role in quality control and product development. With UV weathering simulation, I can evaluate material performance before it ever reaches the field, helping prevent issues that might only appear after extended real-world use.
What Makes the UV Weathering Test Chamber Essential?
Over the years, I’ve worked with a wide range of testing technologies, and nothing provides the same level of controlled accuracy as the UV Weathering Test Chamber. Manufactured with precision by Pacorr, this chamber replicates outdoor environmental conditions using fluorescent UV lamps, condensation systems, and temperature control mechanisms. The chamber is built to imitate the daily cycle of sunlight and dew, which are two of the primary causes of material degradation over time.
By exposing test samples to ultraviolet radiation and periodic moisture, I can measure critical factors like gloss loss, color fading, cracking, chalking, brittleness, and structural failure. It’s not just about simulating damage it’s about understanding failure modes at the molecular level. The controlled environment eliminates variables that could skew natural exposure testing, offering repeatable results that I can depend on to guide production decisions.
UV Light Accelerated Weathering Tester: Predicting Years in Days
Another core instrument I use is the UV Light Accelerated Weathering Tester. This machine offers a faster route to insights. Rather than waiting for seasons to pass, this device can simulate years of environmental wear in a matter of weeks. What I particularly value about this tool is its ability to integrate moisture, UV light, and temperature changes in a cycling pattern that closely mirrors real-world exposure.
At Pacorr, our systems are designed to ensure precise irradiance levels and consistent test parameters, which allows me to compare data across different materials and product iterations. This is especially useful during product development stages when clients need rapid validation on new material blends or coatings. The accelerated data helps prevent costly recalls and reduces the need for extensive field testing.
How International Standards Shape My Testing Process
Following industry-specific standards is non-negotiable for the work I do. They ensure that testing outcomes are credible, comparable, and in many cases, legally compliant. At Pacorr, every chamber and tester is calibrated to meet the strictest global standards.
ISO 16474-1 & ISO 16474-3: The Backbone of Artificial Weathering
These two ISO standards define the general principles and specific methods for exposing materials to artificial UV radiation and moisture. I refer to ISO 16474-1 when outlining the core procedures and to ISO 16474-3 for the specific requirements concerning fluorescent UV lamps. These standards guide me in creating reliable and consistent exposure cycles that yield meaningful degradation results for coatings, plastics, and composites.
ISO 11507: Focused Testing for Paints and Varnishes
Whenever I test decorative coatings, architectural paints, or industrial finishes, I turn to ISO 11507. This standard is specifically tailored for paint and varnish applications, ensuring that parameters such as gloss, adhesion, and surface defects are measured under realistic artificial conditions. With Pacorr’s precise UV testing instruments, I can monitor even the slightest changes in coating performance, helping clients fine-tune formulations for better longevity.
ISO 4892-1 & ISO 4892-3: UV Exposure for Plastics
In polymer and plastic testing, these standards are essential. ISO 4892-1 lays down general principles for UV testing of plastics, while ISO 4892-3 focuses specifically on testing using fluorescent UV lamps. These protocols allow me to evaluate color fastness, mechanical stability, and UV-induced chemical changes in polymers. With Pacorr’s chambers, I can simulate condensation, temperature swings, and UV rays with remarkable accuracy.
ASTM Protocols and Their Practical Relevance
Across many of my testing procedures, ASTM standards act as a bridge between lab conditions and real-world performance. ASTM D4587 is what I refer to for coatings, while ASTM D4329 is tailored for plastic materials. Both offer structured test cycles that align well with the equipment developed by Pacorr.
Additionally, ASTM G151 and ASTM G154 provide overarching guidance for using artificial light sources in weathering equipment. They’re especially useful when I’m customizing exposure cycles to match geographic or application-specific demands. With these standards integrated into Pacorr’s product development, I can confidently simulate everything from high-altitude UV stress to tropical humidity conditions.
Automotive Weathering: Meeting Industry-Specific Needs
Working with automotive materials introduces a different level of complexity. Components must withstand constant UV exposure, interior heat build-up, and frequent temperature cycling all while maintaining appearance and structural integrity. Standards like BS 2782: Part 5, SAE J2020, and JIS D 0205 are my go-to references when validating materials for automotive interiors and exteriors.
With Pacorr’s advanced UV testing chambers, I’m able to mirror conditions specific to different markets whether it’s dry desert sun, humid coastal climates, or freeze-thaw cycles. Our instruments make it easier for manufacturers to meet global quality benchmarks and confidently launch products in diverse geographies.
Why UV Weathering Testing with Pacorr Goes Beyond Compliance
While standards are critical, my approach goes deeper. I see UV weathering testing not just as a box to check, but as a proactive strategy. With Pacorr’s technology, I’m able to give clients insights that lead to stronger product designs, fewer customer complaints, and reduced warranty claims. Every test helps answer the fundamental question: “Will this product last?”
From color retention in branding materials to maintaining clarity in optical plastics, from gloss stability in coatings to crack resistance in automotive dashboards every application benefits from the data generated in our UV chambers.
Pacorr’s Commitment to Precision and Innovation
At Pacorr, we don’t just manufacture instruments we build trust. Each UV Weathering Test Chamber and Accelerated UV Tester is crafted with accuracy, durability, and user-experience in mind. Our commitment to quality is reflected in the consistency of our results and the repeatability of our test conditions.
Having worked with Pacorr’s equipment for years, I can confidently say these instruments deliver more than data they deliver confidence. And in the fast-moving world of manufacturing, that makes all the difference.
Conclusion: Building Durable Products Starts with Reliable Testing
Durability isn’t something that can be left to chance. It’s engineered, tested, and proven inside high-performance UV weathering chambers, under the scrutiny of international standards, and with the precision of instruments I trust every day. At Pacorr, I’m proud to be part of that process, delivering reliable insights that strengthen materials, support innovation, and ultimately protect the end user’s trust.
Thanks to Pacorr Testing instruments, we have all the required quality testing instruments that have helped us to ensure the best quality delivered to our clients.
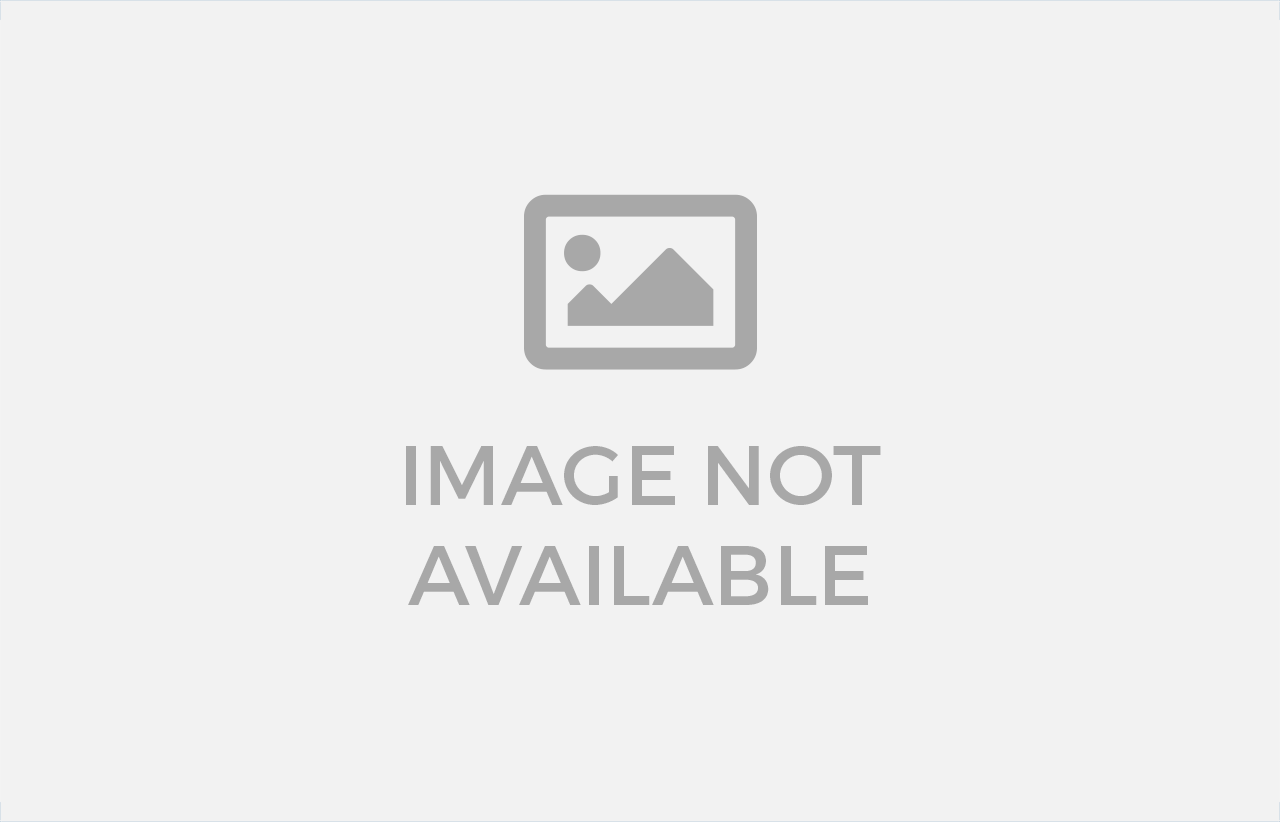
Danish
Fair Exports Pvt. Ltd.