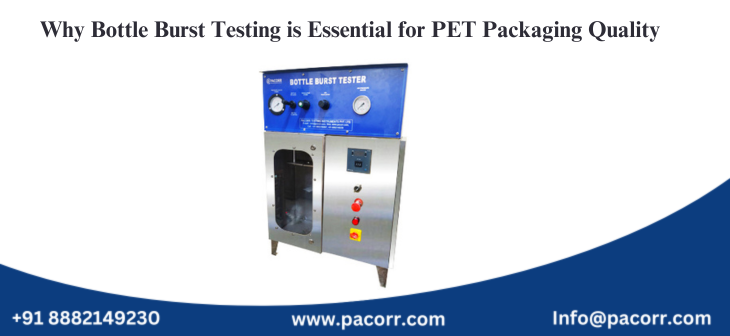
PET (Polyethylene Terephthalate) bottles have become the preferred packaging solution across industries such as beverages, pharmaceuticals, cosmetics, and chemicals due to their lightweight, durable, and recyclable nature. However, ensuring their structural integrity is crucial to avoid product failures, leaks, or potential hazards.
One of the most effective quality control tests for PET bottles is bottle burst testing. This test assesses the maximum internal pressure a bottle can withstand before it ruptures, ensuring it is strong enough to handle real-world conditions such as carbonation pressure, transportation stress, and temperature variations.
In this blog, we will explore the importance of bottle burst testing, how it works, industry standards, and the benefits it provides for PET packaging manufacturers.
What is Bottle Burst Testing?
Bottle burst testing is a critical quality control process used to determine the strength and durability of PET bottles. It involves pressurizing the bottle internally until it bursts, helping manufacturers understand the bottle’s maximum pressure resistance and structural weaknesses.
This test is especially crucial for bottles containing carbonated drinks, chemicals, or high-pressure liquids, as any failure in the packaging can lead to leakage, contamination, or safety risks.
The key objectives of bottle burst testing include:
- Ensuring the bottle withstands internal pressure without deforming or bursting.
- Detecting weak spots in the bottle’s structure.
- Confirming compliance with international quality standards.
- Optimizing material usage for cost-effective production.
The Process of Bottle Burst Testing
Bottle burst testing is performed using a specialized bottle burst tester, which subjects PET bottles to controlled internal pressure until they reach their breaking point. The process involves the following steps:
1. Sample Preparation
- The PET bottle is placed in the testing chamber and securely clamped.
- It is either filled with pressurized air or liquid to simulate real-world stress conditions.
2. Gradual Pressure Application
- The pressure inside the bottle is gradually increased at a controlled rate.
- The test can be customized for different pressure levels, depending on the type and intended use of the bottle.
3. Burst Point Detection
- The pressure is increased until the bottle ruptures or deforms significantly.
- The burst pressure value is recorded to determine if the bottle meets the required quality standards.
4. Analysis and Quality Improvement
If a bottle fails below the required threshold, modifications are made to improve:
- Material composition
- Blow molding parameters
- Bottle design and thickness
Why is Bottle Burst Testing Important?
Prevents Leakage and Product Loss
A weak PET bottle can rupture under pressure, leading to product leakage, contamination, and financial losses. Bottle burst testing ensures that bottles are strong enough to hold liquids without failure, reducing spoilage and recalls.
Enhances Consumer Safety
If a PET bottle bursts unexpectedly, it can cause injuries to consumers and workers. This is especially critical for carbonated beverages and pressurized liquids that experience high internal pressure. By conducting bottle burst testing, manufacturers can prevent potential safety hazards.
Ensures Compliance with Industry Standards
International quality control regulations require PET bottle manufacturers to meet specific burst resistance levels. Some important standards include:
- ASTM C147-86 – Standard Test for Internal Pressure Resistance of Containers
- IS 14543 – Indian Standard for Packaged Drinking Water Bottles
- ISO 9001:2015 – Quality Management Standards
By conducting bottle burst tests, manufacturers can ensure their products meet regulatory requirements, avoiding penalties, legal issues, and brand reputation damage.
Optimizes Material Usage & Reduces Costs
PET bottle manufacturers aim to use the least amount of plastic while maintaining sufficient strength. Bottle burst testing helps in:
- Determining the optimal material thickness
- Reducing excess plastic usage without compromising quality
- Minimizing production costs and environmental impact
Improves Packaging Performance During Transportation & Storage
PET bottles undergo various stresses during transportation and storage, including:
- Stacking in warehouses and retail shelves
- Exposure to extreme temperatures
- Handling during logistics and distribution
By testing bottles under simulated pressure conditions, manufacturers can ensure durability throughout the supply chain, reducing breakage risks.
Key Features of an Advanced Bottle Burst Tester
To obtain precise and consistent results, manufacturers must invest in a high-quality bottle burst tester. The ideal testing machine should offer:
- Automated pressure control for accurate testing
- Customizable settings to test different bottle sizes and materials
- Real-time data monitoring for analysis and reporting
- Leak-proof clamping systems to prevent errors during testing
- Compliance with global quality testing standards
At Pacorr, we offer state-of-the-art bottle burst testers that provide unparalleled accuracy, reliability, and efficiency. Our machines are designed to help manufacturers maintain high-quality PET packaging standards while reducing costs and material wastage.
Bottle burst testing is an indispensable quality control process for PET bottle manufacturers, ensuring packaging is strong, safe, and compliant with industry regulations. By integrating this test into the manufacturing process, companies can:
- Prevent leaks and product loss
- Ensure consumer safety and regulatory compliance
- Optimize raw material usage and reduce costs
- Enhance bottle durability during transportation and storage
At Pacorr, we specialize in providing high-precision testing instruments that empower manufacturers to produce superior PET packaging solutions.
Looking for a reliable bottle burst tester? Visit www.pacorr.com to explore our advanced range of PET bottle testing equipment.
Upgrade your quality control process with Pacorr’s cutting-edge testing solutions today!
Thanks to Pacorr Testing instruments, we have all the required quality testing instruments that have helped us to ensure the best quality delivered to our clients.
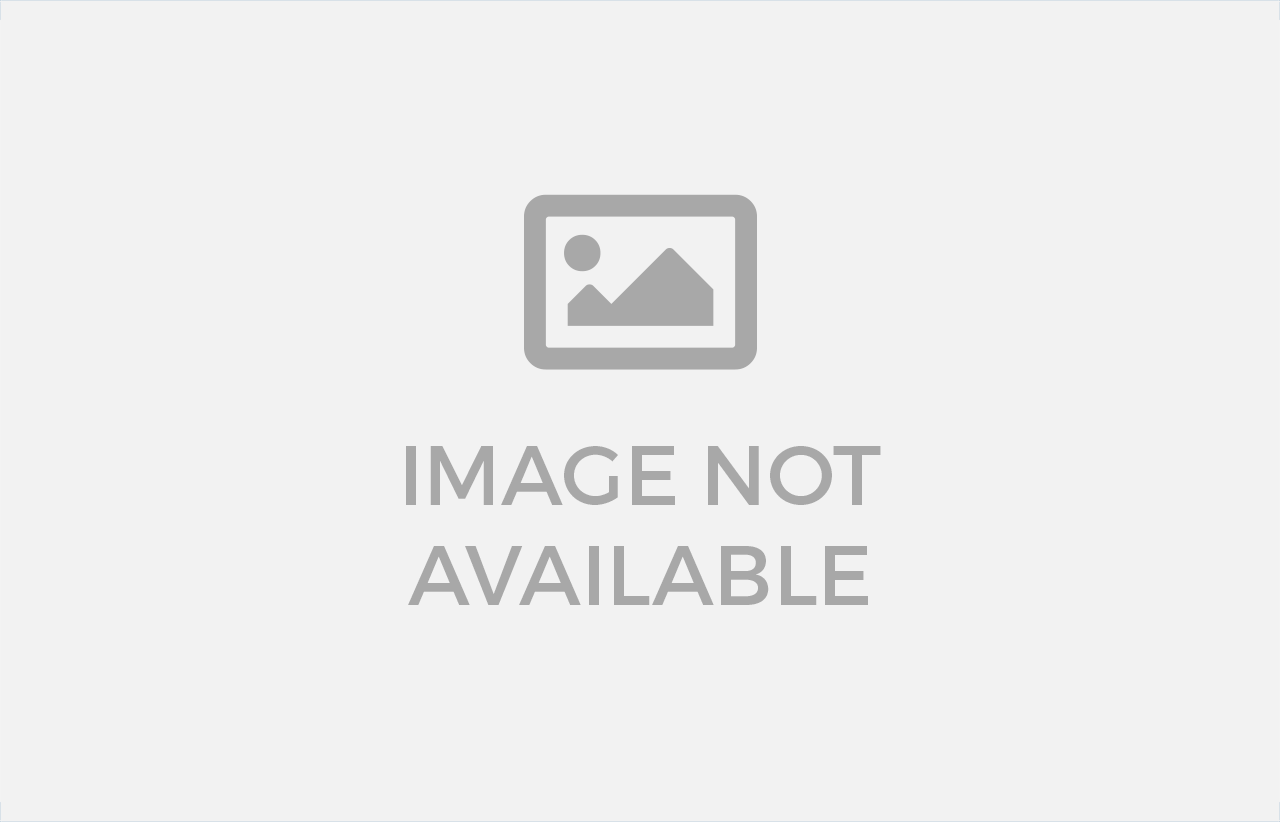
Danish
Fair Exports Pvt. Ltd.