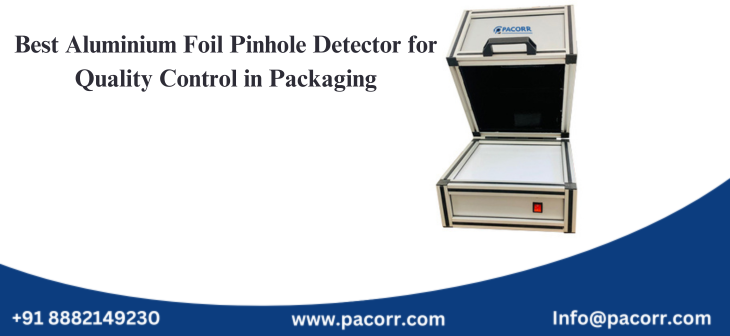
Aluminium foil is a critical material used across various industries, including food packaging, pharmaceuticals, electronics, and insulation. Its primary function is to act as a protective barrier against moisture, light, oxygen, and contaminants. However, even the smallest pinholes in aluminium foil can compromise its protective qualities, leading to potential product damage, contamination, or reduced shelf life.
To maintain high-quality standards, manufacturers utilize pinhole testers for aluminium foil to identify and eliminate such defects before the product reaches the consumer. This in-depth guide will explore everything related to pinhole testing in aluminium foil, including its importance, methods, equipment, and industry applications.
Understanding Pinhole Testing in Aluminium Foil
Pinhole testing is a non-destructive quality inspection process that detects tiny perforations or defects in aluminium foil. These defects, often microscopic and invisible to the naked eye, occur due to several factors, such as material impurities, mechanical stress, or variations in the rolling process.
The purpose of pinhole detection equipment for foil is to ensure structural integrity by detecting and measuring these minute perforations, allowing manufacturers to rectify issues before final packaging.
How Do Pinholes Occur in Aluminium Foil?
The occurrence of pinholes in aluminium foil is influenced by various production-related factors, including:
- Material Composition: Low-purity aluminium may contain impurities, increasing the chances of defect formation.
- Rolling Process: As the aluminium foil undergoes thickness reduction, mechanical stresses may create weak spots leading to pinholes.
- Manufacturing Conditions: Uneven temperature and pressure variations in rolling mills can contribute to defects.
- Handling & Storage: Rough handling and improper storage can cause minor abrasions that develop into full-fledged pinholes.
- Environmental Exposure: Moisture, oxidation, and external contaminants may degrade the foil’s structural integrity over time.
Given these challenges, pinhole testing is an essential step to ensure high-performance packaging solutions.
Why is Pinhole Testing Important in Aluminium Foil?
The importance of pinhole testing in aluminium foil extends beyond just quality assurance; it plays a crucial role in ensuring product safety, regulatory compliance, and consumer satisfaction.
Key Benefits of Pinhole Testing
1. Enhances Barrier Protection:
- Aluminium foil acts as an oxygen, moisture, and light barrier. Any pinhole compromises this function, making products susceptible to contamination and spoilage.
2. Ensures Regulatory Compliance:
- Industries such as food and pharmaceuticals are governed by strict quality control regulations. Pinhole testing machines help manufacturers meet ISO, ASTM, and FDA standards.
3. Prevents Product Contamination:
- Sterile and moisture-sensitive products, like pharmaceutical drugs, rely on aluminium foil as a protective layer. A compromised foil may lead to contamination, posing serious health risks.
4. Increases Customer Trust:
- High-quality packaging builds consumer confidence in a brand. Companies that invest in industrial pinhole detection for packaging foil in QC establish reliability and credibility.
5. Reduces Production Losses:
- Detecting pinholes before product packaging prevents wastage and costly recalls, saving manufacturers from financial setbacks.
6. Optimizes Manufacturing Efficiency:
- By integrating automated pinhole detection systems, manufacturers can streamline production, ensuring higher output with reduced defects.
How to Test Pinholes in Aluminium Foil?
Testing pinholes in aluminium foil requires high-precision detection equipment capable of identifying even the smallest perforations.
Step-by-Step Pinhole Testing Process
1. Preparation:
- A sample of aluminium foil is selected for testing.
- The sample is cut to fit the testing equipment.
2. Testing Phase:
- The aluminium foil pinhole detector scans the material using high-voltage detection, optical inspection, or airflow analysis.
- The machine identifies even the smallest holes that are not visible to the naked eye.
3. Defect Analysis:
- The detected pinholes are measured based on size and distribution.
- Reports are generated to determine whether the foil meets quality control standards.
4. Final Inspection and Quality Check:
- If pinholes exceed the acceptable limit, the batch is rejected or reprocessed.
- If the foil passes the test, it is approved for packaging applications.
Using advanced pinhole testing machines for aluminium foil, manufacturers can eliminate defects before reaching the market.
Types of Pinhole Testing Machines for Aluminium Foil
Modern pinhole detection equipment for foil incorporates automated, non-destructive testing techniques for accurate results. Some of the most common types of pinhole testers include:
1. High-Voltage Pinhole Testers
- Works on the principle of electrical conductivity.
- Detects even the tiniest perforations by passing a high-voltage current through the foil.
- Ideal for pharmaceutical and food packaging applications.
2. Optical Pinhole Detection Systems
- Uses light-based scanning to detect pinholes in the aluminium foil.
- Highly sensitive and accurate, making it perfect for high-speed production lines.
3. Airflow-Based Pinhole Testing Machines
- Measures air leakage through the foil.
- Used primarily for quality control in flexible packaging applications.
4. Automated Industrial Pinhole Detection Systems
- Integrated into production lines for continuous quality monitoring.
- AI-based defect analysis allows for real-time rejection of defective material.
Manufacturers seeking the best pinhole tester for aluminium packaging should consider automation, accuracy, and production volume.
Pinhole Testing Machine Price for Aluminium Foil
The price of a pinhole testing machine varies based on several factors, including:
- Technology Used – High-voltage vs. optical vs. airflow-based detection.
- Testing Speed – Faster machines offer higher throughput, making them costlier.
- Automation Level – Fully automated systems are more expensive but improve efficiency.
- Brand & Warranty – Reliable brands offer better support and durability.
Investing in high-quality pinhole testing equipment ensures long-term cost savings by reducing defective packaging and improving product safety.
Aluminium Foil Pinhole Inspection Process in Industrial Applications
Industries that depend on aluminium foil for packaging must follow a structured pinhole inspection process:
- Material Selection – High-quality aluminium is chosen to reduce pinhole formation.
- Production Monitoring – Automated pinhole detection systems are used during manufacturing.
- Quality Control & Reporting – Test results are documented, and defects are analyzed.
- Final Packaging & Approval – Only approved aluminium foil is used in final product packaging.
This rigorous testing process guarantees defect-free aluminium foil for critical applications.
Conclusion: Ensuring High-Quality Aluminium Foil with Pinhole Testing
Pinhole testing is a crucial aspect of quality control in aluminium foil manufacturing. Investing in advanced pinhole detection equipment for foil ensures product safety, regulatory compliance, and high packaging integrity.
At Pacorr, we provide cutting-edge pinhole testing solutions that help manufacturers enhance quality control and eliminate defects.
Looking for Reliable Pinhole Testing Equipment?
Explore our range of high-precision aluminium foil testing machines at Pacorr and improve your packaging quality assurance today!
Thanks to Pacorr Testing instruments, we have all the required quality testing instruments that have helped us to ensure the best quality delivered to our clients.
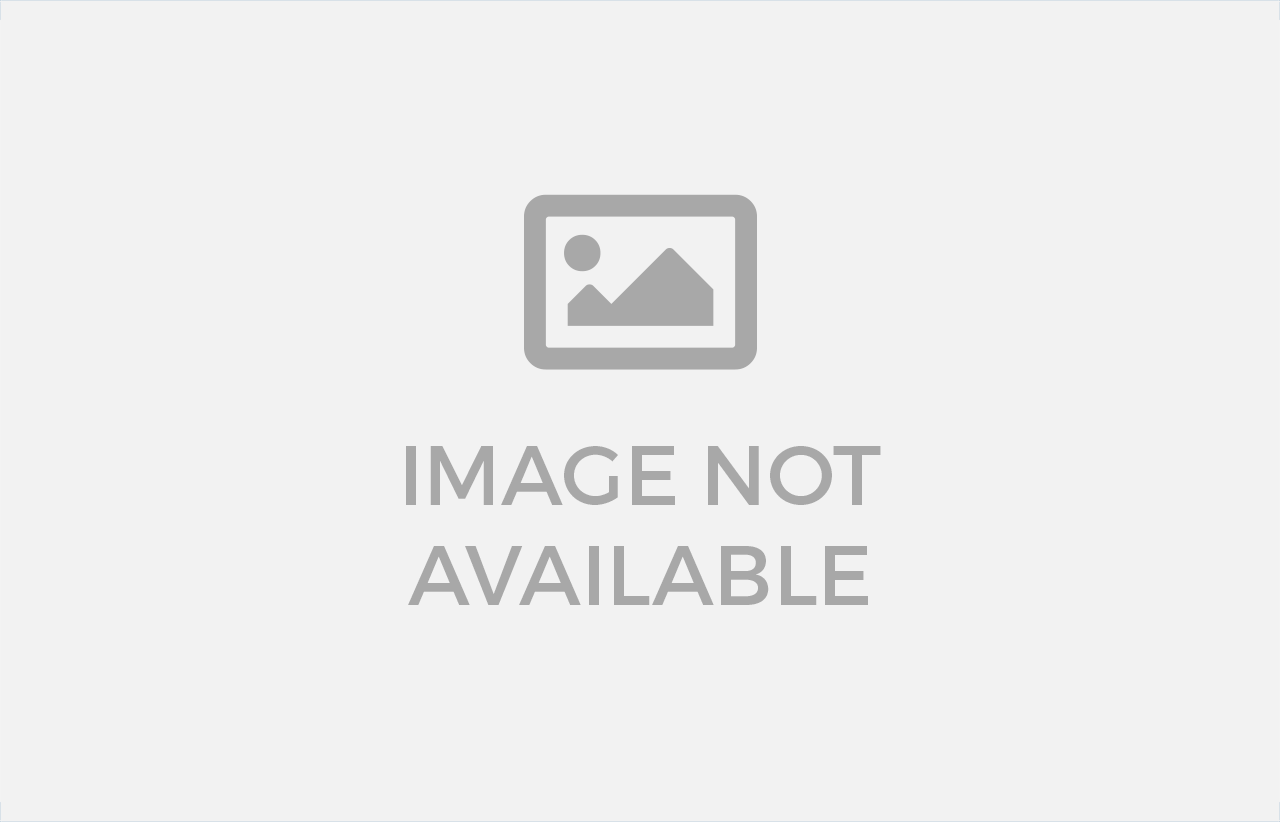
Danish
Fair Exports Pvt. Ltd.