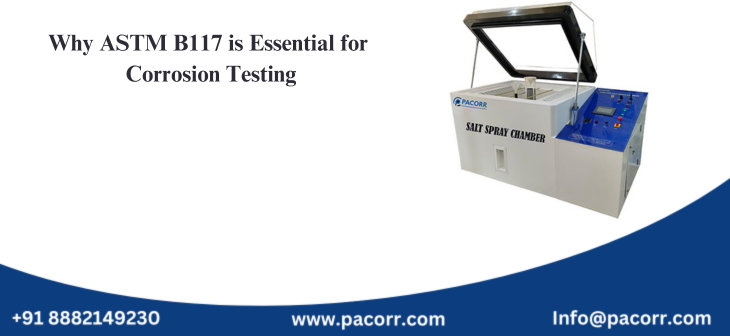
Corrosion can be a costly issue across industries that rely on metals and alloys. Whether you’re working in the automotive, marine, aerospace, or construction industry, ensuring the durability and longevity of metal components is critical to maintaining product quality and safety. ASTM B117 is the industry-standard test method for evaluating the corrosion resistance of materials exposed to salt spray, a procedure known as salt fog or salt spray testing. First established in 1939 by the American Society for Testing and Materials (ASTM), ASTM B117 has become an invaluable benchmark for determining the corrosion resilience of metals, coatings, and finishes. Understanding ASTM B117 can help manufacturers ensure that their products can withstand harsh environments, providing customers with durable and reliable products.
This guide will walk you through the main features, benefits, and applications of ASTM B117, explaining how it works, why it's widely adopted, and real-world applications that highlight its value.
What is ASTM B117? An Overview
ASTM B117 is a standardized test method for conducting salt spray (or salt fog) tests on various materials, primarily metals. The test exposes samples to a controlled corrosive environment, simulating the effects of salt exposure over time. A salt spray test chamber creates an environment filled with a saltwater mist, which accelerates corrosion on the sample surface. The process allows for a rapid assessment of how well materials, coatings, and surface finishes can resist corrosion.
Key Features of ASTM B117 Salt Spray Testing
- Controlled Environment: Test chambers maintain a consistent saltwater mist concentration, pH, and temperature, ensuring a reliable testing environment.
- Accelerated Testing: The exposure to salt spray simulates years of environmental exposure in a fraction of the time.
- Objective Comparison: ASTM B117 enables standardized comparisons between materials, making it easy to evaluate product performance against industry benchmarks.
The Benefits of ASTM B117 Testing
Using ASTM B117 has a range of advantages for manufacturers and suppliers, as it helps in understanding product durability and corrosion resistance. Here are the top benefits:
Enhanced Product Durability
Salt spray testing under ASTM B117 standards helps manufacturers improve product durability by identifying weak points in materials or coatings that may not withstand prolonged exposure to corrosive environments.
Reduced Long-Term Costs
Products that fail due to corrosion lead to increased costs, from replacement to maintenance expenses. ASTM B117 allows manufacturers to address these issues early, potentially reducing long-term expenses associated with product failures.
Competitive Edge
Companies that test their products to ASTM B117 standards often market this certification as a guarantee of quality, which can serve as a competitive differentiator, especially in industries where environmental resilience is paramount.
Quality Control
ASTM B117 can also function as a quality control tool for companies to check the consistency and effectiveness of protective coatings or treatments on metal products.
Compliance with Industry Standards
Many industries mandate corrosion testing as part of their quality or regulatory requirements. By adhering to ASTM B117 standards, companies can easily demonstrate compliance with both industry and client specifications.
How is ASTM B117 Testing Conducted?
The ASTM B117 test procedure is a controlled and repeatable process designed to create a salt fog environment that promotes corrosion. Here’s a brief overview of how the testing works:
- Preparation: Test specimens are cleaned and prepared to ensure that contaminants don’t interfere with results.
- Positioning in Chamber: Specimens are placed in a salt spray chamber, ensuring they are positioned at an angle to maximize exposure to the salt mist.
- Solution Preparation: A 5% salt solution (typically sodium chloride) is prepared to create the salt fog. The pH of the solution is carefully adjusted to between 6.5 and 7.2.
- Environmental Control: The test chamber is set to maintain a temperature of 35°C (95°F) to simulate conditions that accelerate corrosion.
- Duration: Tests can vary in duration, from a few hours to hundreds of hours, depending on the material’s intended application and resistance requirements.
Duration and Interpretation of Results
The length of the test and the results vary according to material type and intended use. For example:
- 48 Hours: Often sufficient for consumer products like kitchen hardware.
- 240 Hours: Commonly used for industrial equipment.
- 1000+ Hours: Required for highly demanding applications, such as aerospace components.
After the test, samples are visually inspected for signs of corrosion, blistering, or other failures. The presence and extent of corrosion can then be used to rate the material’s performance.
Applications of ASTM B117 Across Industries
Salt spray testing is widely used across different sectors to ensure that products meet corrosion-resistance standards. Here’s how ASTM B117 testing is applied in real-world scenarios:
Automotive Industry
Car manufacturers use ASTM B117 to test components like body panels, frames, and hardware. This ensures the vehicle can withstand road salts and environmental exposure without premature corrosion.
Marine Industry
Marine environments expose metals to corrosive saltwater regularly, so ASTM B117 testing is crucial for components like ship hulls, propellers, and structural frames.
Aerospace and Defense
Aircraft and defense equipment often operate in extreme environments. Salt spray testing helps in evaluating corrosion resistance in various metal alloys used in aircraft frames, engines, and defense equipment.
Electronics and Electrical Components
Electrical housings and connectors exposed to harsh outdoor environments must resist corrosion to prevent failure. ASTM B117 helps electronics manufacturers verify that their products can survive these challenging conditions.
Building and Construction
For outdoor structures like bridges, railings, and metal fixtures, ASTM B117 testing confirms that materials and coatings can withstand prolonged exposure to the elements, reducing maintenance costs and improving structural integrity.
Real-World Success: Case Study of ASTM B117 in Action
A leading manufacturer of industrial machinery sought to improve the longevity of its products, as clients in the oil and gas sector reported significant corrosion issues. By incorporating ASTM B117 testing into their product development, the company identified weak points in their coating materials and switched to a more resilient formula. As a result, product lifespan improved by 25%, and customer complaints regarding corrosion dropped significantly. This led to both cost savings and stronger client relationships, as the company could market its products as ASTM B117-certified for corrosion resistance.
Thanks to Pacorr Testing instruments, we have all the required quality testing instruments that have helped us to ensure the best quality delivered to our clients.
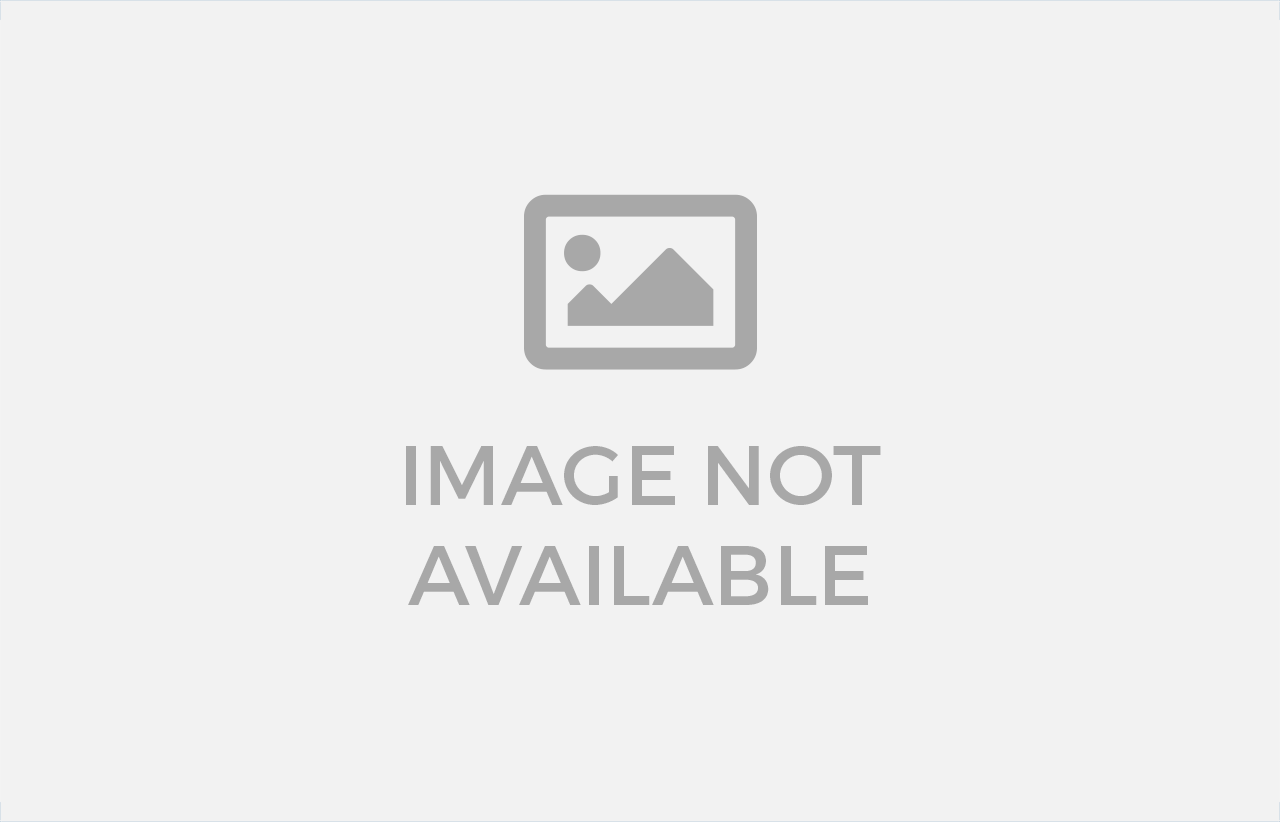
Danish
Fair Exports Pvt. Ltd.