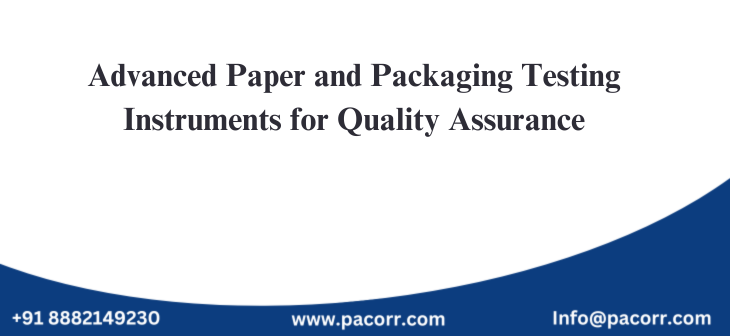
The paper and packaging industry serves as a cornerstone of product preservation, safe transportation, and consumer satisfaction. As the demand for reliable and durable materials grows, the need for effective quality control becomes increasingly evident. Testing instruments offer precision in assessing the integrity, strength, and overall performance of packaging materials, ensuring compliance with international standards. Below is a detailed exploration of these essential instruments and their applications.
The Role of Testing Instruments in Packaging
A packaging material must protect the product from external damage, maintain its form during transit, and present itself attractively to consumers. Any failure in these aspects can lead to financial loss, customer dissatisfaction, or even safety concerns. Testing instruments help in identifying weaknesses, improving material formulations, and delivering a product that stands up to real-world challenges.
Tensile Strength Tester
A tensile strength tester determines the maximum load that a material can bear before breaking. By assessing tensile properties, manufacturers can design materials that offer superior durability and resistance to stretching forces. This ensures that packaging materials like plastic films and paperboards retain their structure during handling and transportation.
Bursting Strength Tester
A bursting strength tester evaluates the ability of paper, cardboard, and other materials to resist rupture under pressure. This test helps determine whether a package can endure external forces during stacking or shipping. A high bursting strength is crucial for maintaining product integrity during transit.
Box Compression Tester
A compression tester measures the load-bearing capacity of boxes and cartons. This test simulates the weight and pressure that packaging may face during stacking in warehouses or transportation. The instrument ensures that a carton can withstand vertical loads without collapsing, providing a reliable safeguard for the product inside.
Cobb Sizing Tester
Water resistance plays a vital role in the performance of packaging materials. A Cobb sizing tester measures the amount of water absorbed by a material within a specified period. This test ensures that the material can maintain its structural integrity even in humid or wet environments, which is essential for packaging food, pharmaceuticals, and other sensitive items.
Coefficient of Friction (COF) Tester
A COF tester analyzes the frictional properties of materials used in packaging films and laminates. This test determines whether the surface of a material offers optimal sliding resistance. A controlled level of friction improves the handling and stacking of packages while maintaining stability during transport.
Environmental Chamber
An environmental chamber creates simulated conditions such as extreme temperatures, high humidity, and sudden environmental shifts. Packaging materials are tested under these conditions to evaluate their durability and performance. This ensures that materials remain reliable under varying storage and transportation environments.
Peel and Seal Strength Tester
A peel and seal strength tester measures the adhesive strength of seals in flexible packaging. This instrument ensures that the seal can endure handling stresses while allowing ease of opening for consumers. Strong seals prevent product contamination, especially in industries such as food and pharmaceuticals.
Drop Tester
A drop tester simulates the effects of accidental drops during handling and transportation. By testing the impact resistance of packaging materials, this instrument helps identify potential vulnerabilities and enables manufacturers to design more robust packaging solutions.
Puncture Resistance Tester
A puncture resistance tester determines the amount of force required to penetrate a material. This test is critical for ensuring that packaging can protect the product from sharp objects or other hazards during shipping. Strong puncture resistance reduces the risk of product damage and ensures consumer satisfaction.
Importance of Testing Instruments in Packaging
- Ensures Quality: Testing instruments provide precise measurements, ensuring packaging meets stringent quality standards.
- Promotes Cost Efficiency: Early detection of material weaknesses reduces waste and prevents costly product returns or recalls.
- Supports Regulatory Compliance: Many industries require packaging materials to meet specific quality benchmarks. Testing instruments help meet these criteria.
- Enhances Consumer Trust: Reliable packaging that withstands real-world conditions boosts consumer confidence and brand reputation.
Pacorr’s Commitment to Excellence
Pacorr specializes in manufacturing high-quality testing instruments for the paper and packaging industry. Every instrument is designed to deliver precise results, ensuring that manufacturers can meet their quality goals. By combining innovation with user-friendly features, Pacorr offers tools that help businesses maintain high standards in packaging durability and performance.
Explore Pacorr’s extensive range of paper and packaging testing solutions at www.pacorr.com and elevate packaging quality with precision-driven tools.
What People Say
Thanks to Pacorr Testing instruments, we have all the required quality testing instruments that have helped us to ensure the best quality delivered to our clients.
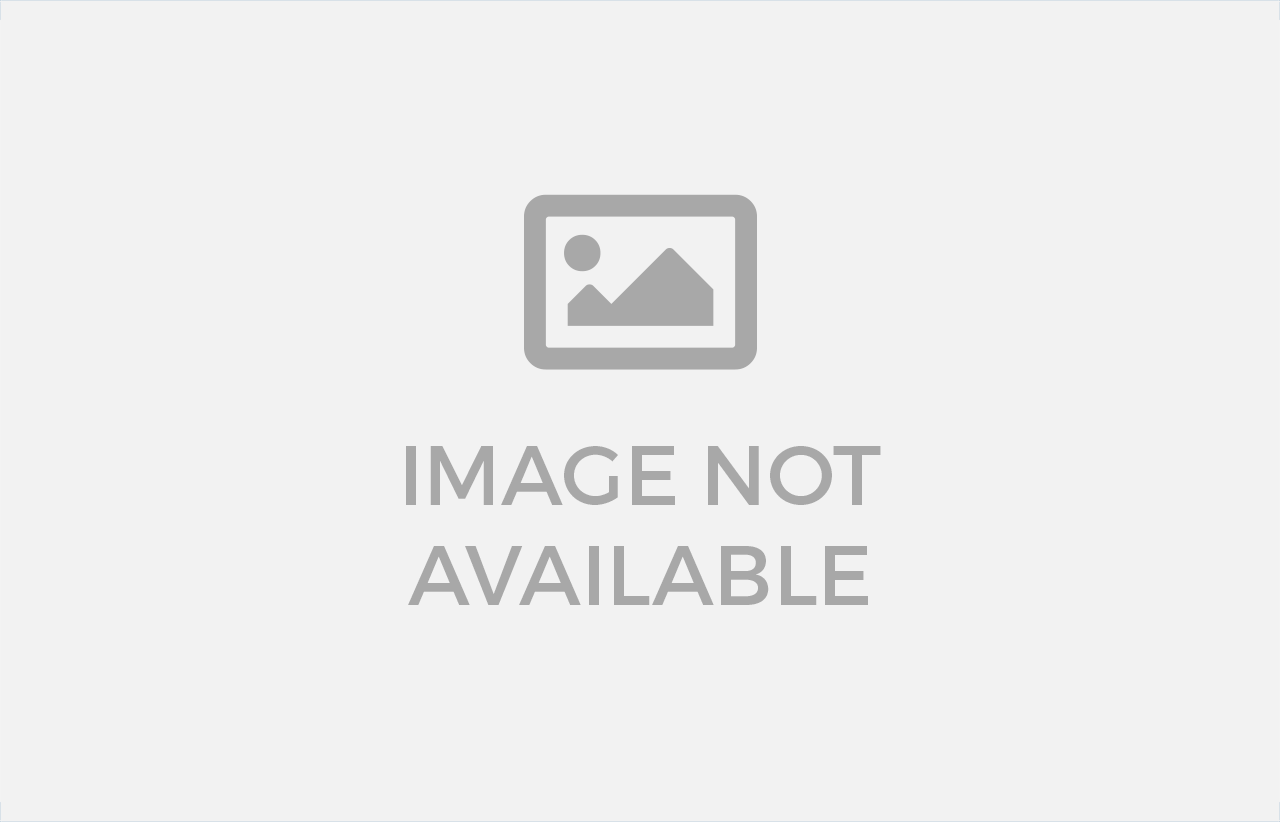
Danish
Fair Exports Pvt. Ltd.