
Advanced Applications of Salt Spray Chamber: Real-World Case Studies in Corrosion Testing
A salt spray chamber is a critical instrument in quality assurance, used for evaluating the corrosion resistance of materials under controlled, simulated environments. Beyond its basic applications, this advanced equipment has become a cornerstone for research, innovation, and performance optimization across industries. By simulating real-world conditions in a laboratory setting, it helps manufacturers refine products, meet regulatory standards, and enhance durability.
This article explores advanced applications of the salt spray chamber through real-world case studies, providing insights into how it has contributed to solving complex challenges in various industries.
Case Study 1: Automotive Sector – Improving Corrosion Resistance in Electric Vehicles
Problem
A leading automobile manufacturer faced a persistent challenge with corrosion in electric vehicle (EV) components, particularly battery enclosures and lightweight materials like aluminum alloys. Winter road salts were causing premature corrosion, compromising the structural integrity and lifespan of these critical components.
Approach
The manufacturer utilized a salt spray chamber to perform cyclic corrosion testing (CCT), which alternates between salt fog exposure, drying, and humidity cycles. This method simulated the harsh environments that EV components encounter during real-world use.
Results
- Material Refinement: The test revealed weaknesses in the protective coatings used on magnesium alloys. This led to the development of a hybrid coating that offered improved resistance.
- Increased Longevity: Battery enclosures were redesigned with a coating system that extended their lifespan by 30%.
- Regulatory Approval: The optimized materials passed stringent international standards, including ISO 9227, ensuring compliance for global markets.
Case Study 2: Aerospace Industry – Addressing Corrosion Fatigue in Aircraft Components
Problem
An aerospace company encountered corrosion fatigue in fuselage panels and fasteners, particularly in regions with high humidity and saline air. This posed safety risks and increased maintenance costs.
Approach
The company used a salt spray chamber to conduct accelerated corrosion testing under simulated stress conditions. Aluminum components were exposed to salt fog and subjected to mechanical stress tests to replicate the simultaneous effects of environmental and operational factors.
Results
- Material Innovation: The study led to the selection of a high-strength aluminum alloy with superior corrosion resistance.
- Safety Enhancements: The new material reduced the risk of corrosion-induced failures by 40%.
- Cost Reduction: Maintenance intervals were extended, resulting in significant cost savings over the aircraft's operational life.
Case Study 3: Marine Applications – Testing Coatings for Offshore Structures
Problem
A marine engineering firm needed to ensure the durability of protective coatings used on offshore wind turbine structures. The high salinity and constant exposure to saltwater posed significant corrosion challenges.
Approach
The firm employed a salt spray chamber to simulate decades of environmental exposure within a short time frame. Coating systems were tested under cyclic conditions involving salt fog, UV radiation, and humidity.
Results
- Enhanced Durability: The testing identified a three-layer epoxy coating system as the most effective, withstanding over 5,000 hours of exposure without degradation.
- Prolonged Service Life: The lifespan of the offshore structures was extended by 15 years.
- Sustainability: The optimized coatings reduced the frequency of maintenance and recoating, lowering the environmental impact.
Case Study 4: Electronics Industry – Protecting Circuit Boards from Corrosion
Problem
An electronics manufacturer experienced high failure rates in printed circuit boards (PCBs) used in outdoor applications. The corrosion of PCBs in coastal environments caused device malfunctions, leading to warranty claims.
Approach
The company conducted tests using a salt spray chamber to expose the PCBs to saline environments and elevated temperatures. This helped identify failure points and guided the development of enhanced conformal coatings.
Results
- Reliability Improvement: The new coating formula improved corrosion resistance by 60%, ensuring consistent performance in challenging environments.
- Market Expansion: The enhanced reliability enabled the company to confidently market its products in coastal regions, increasing sales by 20%.
- Reduced Returns: The improvement in product quality significantly lowered the rate of warranty claims.
Case Study 5: Construction Materials – Evaluating Steel Reinforcement for Bridges
Problem
A construction company needed to test the corrosion resistance of reinforced steel used in bridge construction. Early signs of rust within five years raised concerns about structural safety and durability.
Approach
The company used a salt spray chamber to assess various protective coatings under accelerated conditions. Chloride exposure and wet-dry cycles were simulated to replicate real-world conditions.
Results
- Optimal Coating Selection: An epoxy-based coating demonstrated superior adhesion and resistance to chloride-induced corrosion.
- Longevity Assurance: The coated steel achieved a projected lifespan of 25 years, aligning with the company's infrastructure goals.
- Cost Efficiency: The need for frequent repairs and maintenance was minimized, resulting in long-term savings.
Case Study 6: Consumer Goods – Rust Prevention in Metal Packaging
Problem
A beverage company observed rust development in metal cans stored in humid environments. This issue affected product aesthetics and raised concerns about consumer trust.
Approach
The company used a salt spray chamber to evaluate different lacquer coatings for the cans. Prolonged exposure to salt fog and humidity was simulated to test the coatings' performance.
Results
- Enhanced Coating Durability: The optimized lacquer provided excellent resistance to corrosion, maintaining the cans’ appearance.
- Improved Brand Perception: Rust-free packaging helped restore consumer confidence and boosted sales by 10%.
- Operational Efficiency: The company reduced production waste caused by rust-damaged cans.
Advanced Testing Techniques Enabled by Salt Spray Chamber
These case studies highlight innovative testing techniques facilitated by salt spray chambers:
- Cyclic Corrosion Testing (CCT): Alternating between salt fog, drying, and humidity to replicate real-world environmental conditions.
- Highly Accelerated Life Testing (HALT): Exposing materials to extreme conditions to identify weak points quickly.
- Simulated Stress Testing: Combining environmental and mechanical stress to evaluate performance under realistic scenarios.
Conclusion
The salt spray chamber plays an indispensable role in advancing material performance and ensuring product reliability. Through the case studies presented, it is evident how diverse industries use this equipment to solve complex challenges, improve product durability, and achieve regulatory compliance. By leveraging its capabilities, manufacturers can optimize processes, enhance product quality, and gain a competitive edge in the market.
Investing in advanced salt spray chambers equips businesses to meet modern-day demands for durability, safety, and sustainability.
Thanks to Pacorr Testing instruments, we have all the required quality testing instruments that have helped us to ensure the best quality delivered to our clients.
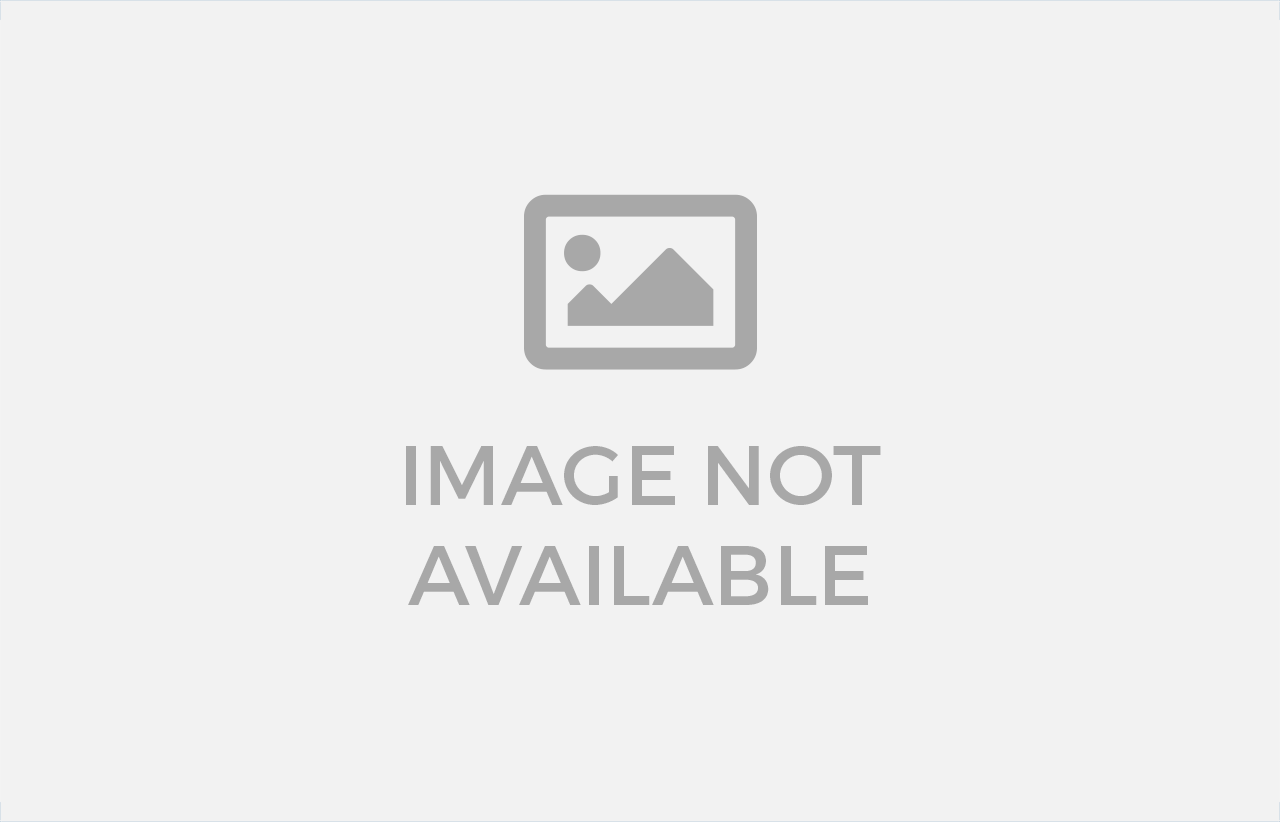
Danish
Fair Exports Pvt. Ltd.